Learn Quality Management
SITE-WIDE SALE IS LIVE NOW.
CLICK HERE.
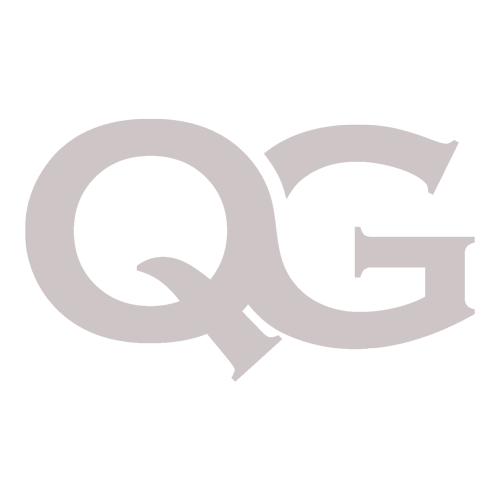
- ASQ® CQA Exam
- ASQ® CQE Exam
- ASQ® CSQP Exam
- ASQ® CSSYB Exam
- ASQ® CSSGB Exam
- ASQ® CSSBB Exam
- ASQ® CMQ/OE Exam
- ASQ® CQT Exam
- ASQ® CQPA Exam
- ASQ® CQIA Exam
- 7 Quality Tools
- Quality Gurus
- ISO 9001:2015
- Quality Cost
- Six Sigma Basics
- Risk Management
- Lean Manufacturing
- Design of Experiments
- Quality Acronyms
- Quality Awareness
- Quality Circles
- Acceptance Sampling
- Measurement System
- APQP + PPAP
- GD&T Symbols
- Project Quality (PMP)
- Full List of Quizzes >>
- Reliability Engineering
- Statistics with Excel
- Statistics with Minitab
- Multiple Regression
- Quality Function Deployment
- Benchmarking
- Statistical Process Control
- Measurement Scales
- Quality Talks >> New
- Six Sigma White Belt
- Six Sigma Yellow Belt
- Six Sigma Green Belt
- Six Sigma Black Belt
- Minitab 17 for Six Sigma
- Casio fx-991MS Calculator
- CSSYB/LSSYB Mock Exam
- CSSGB/LSSGB Mock Exam
- CSSBB/LSSBB Mock Exam
- ASQ® CCQM Preparation
- ASQ® CQA Preparation
- ASQ® CQE Preparation
- ASQ® CQPA Preparation
- ASQ® CQIA Preparation
- CQE Mock Exams
- CMQ/OE Mock Exams
- CQA Mock Exams
- CQIA Mock Exams
- CQPA Mock Exam
- CQT Mock Exam
- CQI Mock Exam
- CSQP Mock Exam
- CCQM Mock Exam
- Design of Experiments (DoE)
- Measurement System Analysis
- Statistics Using R
- Data Visualization with R
- Statistics Using Python
- Data Visualization with Python
- Regression with Minitab
- Logistic Regression
- Data Analysis Using Excel
- The Git Mindset
- Statistics Quiz
- Root Cause Analysis
- Kano Analysis
- Lean Management
- QMS Lead Auditor
- Quality Management
- ISO 9001:2015 Transition
- Project Quality Manager
- गुणवत्ता.org
- Summary Sheets
- Practice Tests
- QG Hall of Fame
- Testimonials – ASQ Exams Preparation
Blogs , ISO 9001
- Quality Control: Understanding Its Importance, Benefits, Approaches and Key Strategies
** Unlock Your Full Potential **
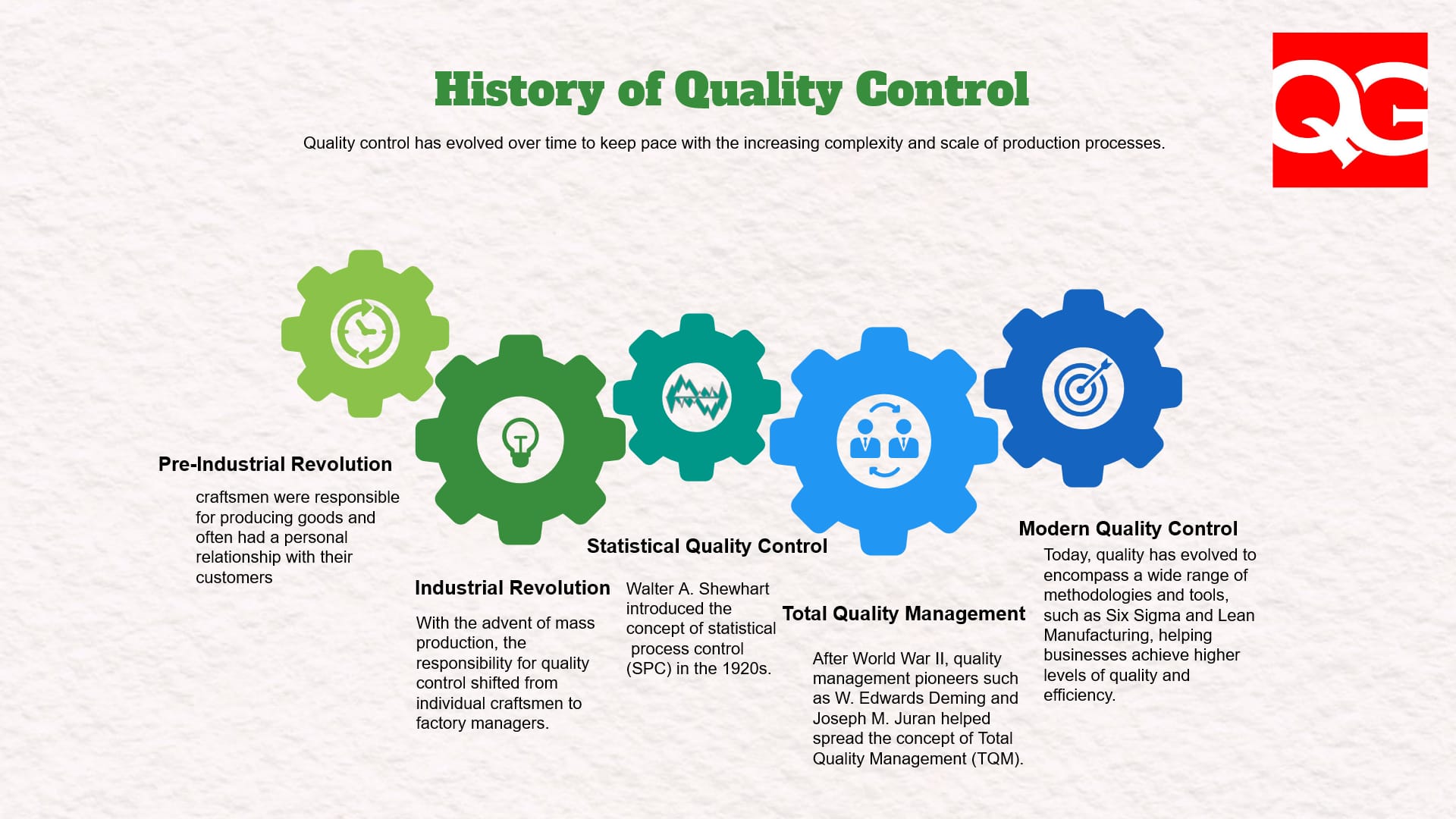
Maintaining high-quality products and services is crucial for success in today's competitive business environment. Quality control (QC) plays a critical role in ensuring that your company consistently meets customer expectations and regulatory requirements. This comprehensive guide will explore the importance of quality control, its benefits, and key strategies, with industry examples to illustrate its practical applications.

What is Quality Control?
Quality control refers to the systematic process of identifying, monitoring and correcting potential defects or deviations in products or services. This process ensures that the final output meets the established quality standards and customer requirements. QC is an essential part of the overall quality management system ( QMS ) and involves regular inspections, testing, and monitoring of various production stages.
ISO 9001:2015 defines Quality Control as “a part of quality management focused on fulfilling quality requirements.” It includes activities such as the inspection and testing of incoming raw materials, in-process products, and finished goods.
History of Quality Control
Quality control has evolved over time to keep pace with the increasing complexity and scale of production processes. Let's take a brief look at the key milestones in the history of quality control:
Craftsmanship Era (Pre-Industrial Revolution): Before the Industrial Revolution, craftsmen were responsible for producing goods and often had a personal relationship with their customers. Quality was maintained by the craftsman's reputation, skill, and pride in their work.
Industrial Revolution (Late 18th Century to Mid-19th Century): With the advent of mass production, the responsibility for quality control shifted from individual craftsmen to factory managers. Inspectors were employed to identify and segregate defective products, but the focus was on finding and fixing defects rather than preventing them.
Scientific Management (Early 20th Century): The introduction of scientific management principles by Frederick Winslow Taylor marked a significant shift in quality control. Taylor's ideas laid the groundwork for more systematic and data-driven approaches to managing production processes, paving the way for modern quality control methods.
Statistical Quality Control (Mid-20th Century): Walter A. Shewhart introduced the concept of statistical process control ( SPC ) in the 1920s. SPC allowed manufacturers to monitor and control production processes using statistical methods, enabling them to detect and correct defects more efficiently. During World War II, the U.S. military adopted statistical quality control techniques to improve the production of munitions and other equipment.
Total Quality Management (Post-WWII): After World War II, quality management pioneers such as W. Edwards Deming and Joseph M. Juran helped spread the concept of Total Quality Management ( TQM ). TQM emphasized continuous improvement, customer satisfaction, and employee involvement, transforming how companies approached quality control.
ISO 9001 and Modern Quality Control (Late 20th Century to Present): In 1987, the International Organization for Standardization (ISO) introduced the ISO 9000 quality management standards, including ISO 9001 . These standards provided a global framework for implementing effective quality management systems. Today, quality has evolved to encompass a wide range of methodologies and tools, such as Six Sigma and Lean Manufacturing, helping businesses achieve higher levels of quality and efficiency.
The history of quality control shows how the concept has evolved and adapted to the changing needs of production processes and market demands. Understanding this history can help businesses appreciate the value of quality control and implement more effective systems to ensure long-term success.
Benefits and Importance of Quality Control
- Customer Satisfaction: Consistently delivering high-quality products and services helps build customer trust and loyalty, increasing the likelihood of repeat business and positive word-of-mouth marketing.
- Regulatory Compliance: QC processes help companies adhere to industry-specific regulations and standards, preventing costly fines or sanctions.
- Brand Reputation: A strong commitment to quality control enhances a company's reputation for producing reliable, high-quality products or services.
- Cost Savings: Identifying and correcting defects early in production minimizes waste and reduces the need for expensive rework or recalls.
- Competitive Advantage: Companies with robust QC systems are better positioned to differentiate themselves from competitors and capture market share.
Key Strategies for Effective Quality Control
- Establish Clear Quality Standards: Define and communicate the specific quality criteria for each product or service, ensuring all team members understand the expectations.
- Implement Regular Inspections and Testing: Conduct routine checks at various stages of production to identify defects and deviations from quality standards.
- Invest in Employee Training: Provide ongoing training to equip employees with the necessary skills and knowledge to maintain high-quality standards.
- Utilize Statistical Process Control ( SPC ): SPC techniques can help identify trends and patterns in production data, enabling companies to predict and prevent quality issues.
- Embrace Continuous Improvement: Encourage a culture that values ongoing learning and improvement and proactively empowers employees to identify and address quality concerns.
Quality Control Approaches
Different industries and organizations may adopt various approaches to quality, depending on their specific needs and goals. Some popular QC methodologies include:
- Total Quality Management ( TQM ): A holistic approach to quality management focuses on continuous improvement, customer satisfaction, and employee involvement. It aims to integrate quality principles into all aspects of a company's operations.
- Six Sigma: Six Sigma is a data-driven quality management methodology seeking to reduce defects and process variation. The goal is to achieve a defect rate of 3.4 per million opportunities, ensuring near-perfect quality.
- Lean Manufacturing: Lean focuses on eliminating waste and optimizing processes to deliver maximum value to customers. Although not explicitly a quality control approach, Lean principles can significantly contribute to improving product quality by enhancing efficiency and reducing defects.
- ISO 9001: This international standard sets out the criteria for a quality management system . Achieving ISO 9001 certification demonstrates a company's commitment to maintaining consistent quality standards and continuously improving its processes.
Conclusion:
Quality control plays a crucial role in ensuring that businesses deliver high-quality products and services, meeting customer expectations and regulatory requirements. Companies can develop and implement effective QC systems that contribute to long-term success by understanding its importance, benefits, and key strategies.
Related Posts:
Qms auditor / lead auditor course (accredited), kano analysis expert – basics to advanced (accredited), certified six sigma yellow belt (cssyb) exam preparation training (accredited), lean six sigma black belt (accredited) certification, lean six sigma white belt (accredited) online training, six reasons why continuous improvement projects fail, asq® cqa [2022] | how to pass your certified quality auditor exam, poka yoke, fool proofing or the mistake proofing, iso 9001 audits: 11 tips for preparation and success, asq® certified supplier quality professional – csqp.
49 Courses on SALE!
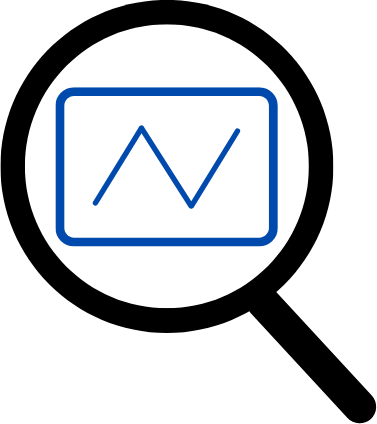
Presentations made painless
- Get Premium
113 Quality Control Essay Topic Ideas & Examples
Inside This Article
Quality control is a critical aspect of any business or organization that aims to deliver high-quality products or services to its customers. It involves monitoring and evaluating the quality of products or services to ensure they meet certain standards and specifications. Quality control is essential to prevent defects, errors, and inconsistencies that can negatively impact a company's reputation and bottom line.
If you're tasked with writing an essay on quality control, you may be struggling to come up with a topic that will engage your readers and demonstrate your understanding of the subject. To help you get started, here are 113 quality control essay topic ideas and examples:
- The importance of quality control in manufacturing
- How quality control can improve customer satisfaction
- The role of quality control in ensuring product safety
- The impact of quality control on a company's reputation
- Best practices for implementing a quality control program
- The benefits of using technology in quality control
- How quality control can help reduce waste and improve efficiency
- The relationship between quality control and quality assurance
- The challenges of implementing quality control in a small business
- The role of statistical analysis in quality control
- Quality control in the food industry: ensuring product safety and freshness
- The impact of globalization on quality control practices
- Quality control in the healthcare industry: ensuring patient safety
- The importance of quality control in the pharmaceutical industry
- How quality control can help prevent product recalls
- Quality control in the automotive industry: ensuring vehicle safety
- The role of quality control in the construction industry
- The impact of quality control on supply chain management
- Quality control in the hospitality industry: ensuring customer satisfaction
- The challenges of implementing quality control in a service-based business
- The role of quality control in ensuring data accuracy and integrity
- Quality control in the retail industry: ensuring product quality and consistency
- The impact of quality control on brand loyalty
- The role of quality control in meeting regulatory requirements
- The benefits of implementing a Total Quality Management (TQM) program
- Quality control in the aerospace industry: ensuring the safety of aircraft
- The impact of quality control on employee morale and motivation
- The challenges of implementing quality control in a fast-paced environment
- Quality control in the technology industry: ensuring software reliability
- The role of quality control in disaster preparedness and response
- The impact of quality control on the environment and sustainability
- Quality control in the education industry: ensuring academic standards
- The benefits of implementing a Six Sigma quality control program
- Quality control in the energy industry: ensuring the safety of power plants
- The role of quality control in the entertainment industry
- The impact of quality control on social responsibility and ethical practices
- Quality control in the fashion industry: ensuring product quality and design
- The challenges of implementing quality control in a global supply chain
- The role of quality control in the financial industry: ensuring data accuracy
- Quality control in the telecommunications industry: ensuring network reliability
- The benefits of implementing a Lean Six Sigma quality control program
- Quality control in the transportation industry: ensuring vehicle safety and maintenance
- The impact of quality control on customer retention and loyalty
- The role of quality control in the healthcare industry: ensuring patient outcomes
- Quality control in the pharmaceutical industry: ensuring drug safety and efficacy
- The challenges of implementing quality control in a regulated industry
- The role of quality control in ensuring product consistency and reliability
- Quality control in the automotive industry: ensuring vehicle performance and safety
- The impact of quality control on employee satisfaction and retention
- The benefits of implementing a Quality Management System (QMS) for quality control
- Quality control in the aerospace industry: ensuring the safety of space missions
- The role of quality control in the construction industry: ensuring building safety
- Quality control in the food industry: ensuring food safety and quality
- The challenges of implementing quality control in a fast-changing market
- The role of quality control in the hospitality industry: ensuring customer satisfaction
- The impact of quality control on brand reputation and customer trust
- The benefits of implementing a quality control program for small businesses
- Quality control in the technology industry: ensuring software reliability and security
- The role of quality control in the energy industry: ensuring the safety of power plants
- Quality control in the education industry: ensuring academic standards and curriculum
- The role of quality control in the entertainment industry: ensuring product quality
- Quality control in the financial industry: ensuring data accuracy and integrity
- Quality control in the telecommunications industry: ensuring network reliability and performance
- The role of quality control in the transportation industry: ensuring vehicle safety
- Quality control in the healthcare industry: ensuring patient safety and outcomes
- The challenges of implementing quality control in a regulated environment
- The role of quality control in the pharmaceutical industry: ensuring drug safety
- Quality control in the food industry: ensuring product safety and quality
In conclusion, quality control is a critical aspect of any business or organization that aims to deliver high-quality products or services to its customers. By selecting a relevant and engaging topic from the list above, you can demonstrate your understanding of quality control and its importance in various industries. Good luck with your essay!
Want to research companies faster?
Instantly access industry insights
Let PitchGrade do this for me
Leverage powerful AI research capabilities
We will create your text and designs for you. Sit back and relax while we do the work.
Explore More Content
- Privacy Policy
- Terms of Service
© 2024 Pitchgrade
Quality management Essay
Introduction, problem and motivation, provisional title, analysis: google swot analysis, improvement options, recommendations.
Bibliography
Quality management activities in organizations are undertaken to ensure that quality in its products is achieved and maintained within an unacceptable budget. It is an activity that is closely dependent on the feedback from the organization’s clients, thus the quality management concept involves establishing channels for relaying customer feedback for which it requires that they function properly through out.
As a part of quality management, the feedback is taken and incorporated in the design of new products that are aimed at raising customer satisfaction. Quality management spans from creating a design and lifecycle plan for a product or service to its production and distribution. The activity involves identifying and measuring process elements, doing performance analysis and applying continuous quality improvements on the products, services and systems of production and distribution.
In this paper, Google, the Internet search giant, is analyzed, and recommendations are made on how it can maintain as well as improve the quality of its products. This is important for the company in maintaining and enhancing its exemplary performance as its pursues its mission, which is to create an Internet resource from which you can access any kind of information disregarding geographical borders. Thus, the problem and motivation in this paper are quality and quality enhancement respectively.
The provisional title that describes the contents of this paper best is “Safeguarding and enhancing quality at Google”.
Brief Review of the related literature
As stated above, quality management activities in organizations are undertaken to ensure that quality in its products is achieved and maintained within an unacceptable budget. The Quality management concept is enriched by eight management principles that are fundamental in improving the performance of an organization. One of these principles is customer focus, which emphasizes to an organization its dependency on its customers and, therefore, highlights the need for it to understand and appreciate their current and future needs for which it should set out to meet.
When an organization achieves customer focus, it implies that it is necessary to know not only both its internal and external customers, but also their needs and quality standards. Another principle is leadership, which facilitates the establishment of unity of purpose among the personnel in an organization. Unity of purpose in an organization is critical in the achievement of its quality objectives and goals.
Involvement of people is another principle that enriches the quality management concept. In an organization, there is the need for its personnel from whatever level to be involved fully in benefiting the organization. The next principle is a process approach, which develops the idea that an organization’s objective is better realized when its activities and allied resources are managed as an organizational process.
The following principle is approaching management as a system so that efficiency and effectiveness in achievement of the organization’s goals are boosted. Continual improvement is another factor that enriches the quality management concept. This principle stresses the need to pursue continued improvement on its product or service to the organization.
Another principle is a factual approach to decision-making, which emphasizes on the need to base decision-making of the organization on data analysis and information. The last principle is the organization having supplier relationships that are mutually benefiting as these increase the ability for it and its suppliers to add value to their product(s) or service(s).
SWOT analysis is a tool used in the managerial activities of corporate organizations that wish to attain stability and sustainability in the long-term. Its use in corporate organization management is aimed at realizing long-term stability and sustainability, specifically in decision-making.
For a given corporate organization, a SWOT analysis procedure takes into account both its internal and external environment to reveal the organization’s strengths, weaknesses, opportunities and threats. The analysis of the corporate organization’s internal environment reveals its strengths and weaknesses whereas that of the external environment reveals its opportunities and threats.
Once the analysis is completed, the SWOT approach is such that a corporate organization will consolidate its strengths, do away with its weaknesses, seize its opportunities and counter its threats. The following is a SWOT analysis for Google Inc., which, as discussed, will reveal the company’s strengths, weaknesses, opportunities and threats.
Aims and objective of the research
In Google’s business model, the company believes in giving users an online experience that eventually leads to strong verbal marketing of the company and continually increasing Internet traffic directed to the company’s products.
The experience is embodied in services to users that are of the best and highest quality; thus, quality is a key issue in Google. The main aim and objective of the research done here is to come up with recommendations that are directed towards helping the company to maintain and enhance the quality of its products.
Statement of the design and methodology
Through a performance and SWOT analysis of Google, we understand the company’s operating environment, and why it is important for it to manage quality in its products.
Company Description
Google Inc. is one of the world’s most successful companies specializing in Internet technology. Originally co-founded by Larry Page and Sergey Brin, the company offers a unique Internet service for which it has established itself as a market leader. Its mission is to provide an Internet resource from which you can access any kind of information disregarding geographical borders.
Google’s business model
Google‘s business model that reflects the company’s mission is unlike that of its competitors. The model stresses on giving users an online experience that eventually leads to strong verbal marketing of the company and continually increasing Internet traffic directed to the company’s products.
The experience is embodied in services to users that are of the best and highest quality. The business model has led Google to make major acquisitions of and alliances with other Internet technology companies that include Amazon, e-bay, Picasa, Keyhole and You Tube.
Google’s collaboration and mergers with other huge online firms make a part of a strategy aimed at ensuring the company always ahead of its business rivals. These acquisitions and mergers have, however, seen the company deviate from its original business model since it has found itself in entirely new markets. Taking into account the source of its revenue, it can be said that Google is mainly an advertising company.
For Google, appealing to its customers means redefining both e-commerce and e-business. Given that its business model stresses on advertisements and provision of services to all the Internet users the company maintains a strategic interest with online markets and firms that attract huge Internet traffic.
Google’s 2010 performance analysis
In 2009, Google Inc. emerged as the worldwide market leader in Internet and mobile search advertising and saw the company ranked fourth by CNNmoney in its list of 100 best companies to work for in 2010. Although not spared by the 2008/9 global financial crisis, the company managed not only to register profits but growth as well as during the period.
Google’s 2010 turnover was slightly under $30 billion, which was a 24% increase using 2009 as the base year. Given the size of the company, the figure implies that the company registered huge growth. The growth is attributed to an increase in click volumes by 18% and a rise in the cost per click by about 5%. The rise in volume can be itself linked to continued development of the company’s network, remarketing and/or the increased use of the Smartphone and tablets.
A further analysis of the turnover reveals that the share of revenue accrued in the U.S remained at 52% whereas that accrued in the U.K slightly declined in the fourth quarter of the year by 2%. However, these had no effect on the overall revenue pattern of the company that remained relatively unchanged. Also, remaining unchanged was how revenue was split: revenue generated from advertisements on Google’s own websites remained at 66% that from advertisement’s on the company’s third party websites remained at 30% and that from other sources remained at 4%.
Google’s strengths
Google’s SWOT analysis reveals its market as one of its strengths. The marketing strategy in use at Google is unique to it and historically, is one of a kind in online technology. Google does not restrain its business ventures to its search engine but is continuously introducing new products into the market.
One of Google’s target markets is the portion of the world’s youth in search for information, fun, knowledge and who wish to be at per with their different environmental surroundings. The other target market is any individual who uses the company’s search engine as he or she knowingly or unknowingly generates revenue for the company indirectly.
The SWOT analysis reveals Google’s key technologies as another of its strengths. One of the company’s key technologies is its search engine whose development process has seen it answer queries more accurately. The software technology incorporated in the search engine enables it perform computations and return results at very advanced speeds. This is unlike traditional search engines whose technology is not as time-sensitive.
The company to examine web content and rank it by level of importance uses Google’s PageRank TM technology boosted by over 200 signals. The architecture of PageRank TM technology is such that it can hold over 500 million variables that in turn can hold 2 billion terms. Due to this architecture it is thus possible for the company to profile web pages and determine those of importance so that they are programmed to appear first on the result page. Google as extended its technology to include Hypertext-Matching Analysis, which performs a full content analysis of text web pages in an effort to return more accurate results for a given query.
The SWOT analysis reveals quality of its personnel as another of Google’s strengths. Google recruitment policy targets individuals of outstanding academic achievements and high experience in the various fields not only of information technology but also of knowledge management.
Top managerial posts at Google are filled with individuals who have an MBA or a PHD in a field that is relevant in enabling the company achieve its mission. To underline further that indeed quality of personnel is another of Google’s strength it can be seen from data collected in 2008 that the company had the highest profit per employee amongst its rivals, which was estimated at $209,624. This figure is further motivation to the employees who are inherently encouraged by the company’s organizational culture to give out their best for the benefit of the company.
The SWOT analysis reveals Google’s capital base and its revenue streams as another of its strengths. 10 years after Google was founded its capitalization rose phenomenally to £105 billion which was enough to replace Procter and Gamble from 5 th place on the US stock market. As stated earlier the main source of Google’s income comes from advertisements done on its site and those done on its third party sites. In 2006, Google was estimated as earning about 30% more on an advert than Yahoo or any other of its rivals does.
Google’s Weaknesses
One of Google’s weakness as revealed by the SWOT analysis is the high rate at which the company receives CVs and Resumes. The rate at which Google’s receives CVs and Resumes is staggering. These results in large volumes of these documents that make it difficult for the company to recruit the best applicants for available positions.
Another of Google’s weaknesses as revealed by the SWOT analysis is external employee turnover of its senior executives. A number of top executives have left Google in favor of Facebook. This exodus of highly skilled personnel from Google can have devastating effects on its future. Furthermore, the company seems not to know how to contain the problem and ironically its proposed measure as aggravated the crisis further.
Another of the company’s weakness as brought out by the SWOT analysis is recruiting a lot of contactors. This habit has led to hiring of contractors who only waste the company’s resources. This is an indication of poor staff recruitment plans and poor job description and evaluation plans. Other weakness of Google are its feeble presence in the social networking market, arbitrary content, too much liquidity, stock problems, material that is heterogeneous, Anglo-Saxon focus, political issues, problems with stock and its inability to generate revenue form You Tube.
Google’s opportunities
An opportunity for Google as revealed by the SWOT analysis is its operating system. Google has set out on a mission to assert its dominance in the operating system market with the Chrome and Android operating systems. The approach by Google is to introduce an operating system that uses applications directly from the Internet as opposed to the traditional approach of operating systems that reside on a PC. Experts who see the Internet as the future of information technology support the approach. This step by Google is seen by some people as a challenge to the current operating system’s market leader, Microsoft.
Other opportunities for Google are new acquisitions and mergers, growth in Internet usage globally, using web content of higher value, reaching new user groups and content, offering a starting point that is easy and more usage of expensive content.
Google’s threats
A threat to Google as revealed by the SWOT analysis is the lawsuits it faces. Yahoo, Amazon and Microsoft are some of the companies that have at different times filed lawsuits against Google. One of the lawsuits filed collectively by these three companies saw Google settle it with an amount of $125 million. Another threat that faces Google as per the SWOT analysis is the company’s failure to motivate its contract employees.
The contract employees are spread in different regions in the world. Other threats to Google are gradually raising competition, privacy issues on content ownership, new technologies, the social networking site Facebook, censorship possibility and the slowdown in ad-spend.
Continual improvement is one of the principles that enrich the quality management concept. The principle stresses the need for a product to be of the best and highest quality. To improve quality in a company like Google, the apt option would be for the company to pursue CQI, which is a recurring process.
Considering Google’s mission and how it plans to achieve it, a suitable procedure for improving quality in the company should be based on FMEA. To add weight to this decision, we consider that the company is continually developing products whose quality has to be improved with time. FMEA was first used by NASA specifically for identifying risks and mitigating their effects; however, the procedure has recently become widespread in industries where it is critical in realizing process improvement. With FMEA, potential failures associated with a product are identified beforehand and action plans formulated to deal with them.
For a given product, the FMEA analysis process begins with identifying potential failures in it. In this step, it is critical to know the set requirements for the product. If potential failures are found, the second step in the procedure is determining the level of severity for each. This is a process that requires a complete picture of the system. The third step in the analytic procedure is knowing the cause of the failures and working out what is known as the probability of occurrence. The fourth step in the analysis procedure is coming up with controls and weighing their effectiveness.
If the controls are associated with risks, it prioritizes them. The fifth and the final step in the analysis procedure is documenting the action plans formulated to deal with each of the risks identified in the previous step. Another option for quality improvement available to Google is Six Sigma strategy, which is built from concepts derived from the statistics and quality engineering fields. Six Sigma is a strategy whose objective is to enhance business success through managing and improving quality. The strategy being a variant of Deming’s Plan-Do-Check-Act Cycle is implemented through two methodologies, namely, DMAIC and DMADV.
In the DMAIC methodology, the first step in improving quality is defining the problems of the existing system taking into account customer opinions. The second step is performing measurements of the current and existing system and collecting data that is relevant to the problem tackled. The third step is analyzing the data collected in the second step to determine the causes of the problem(s) and their effects.
The fourth step is improving the current and existing system by implementing the recommendations made from studying the problem. The fifth step is controlling future state processes so as to ensure that deviations from the required quality standards are corrected before finding their way to finished product. In the DMADV methodology, the first step in improving quality is designing goals that reflect or capture the opinions of the customers. The second step is measuring the current system and identifying CTQs. The fourth step is analysis and development of alternatives to the design.
The fifth step is optimizing the design developed and preparing it for verification. The fifth step is design verification where the design is tested, implemented and submitted to the project owners who initiated it.
A recommendation to Google is for the company to adopt an FMEA based approach to quality improvement. The main shortcoming of the FMEA approach is that the activity is quite costly to implement on each and every product. However, considering its benefits and Google’s capital base, cost is not really an issue.
A recommendation to Google is for the company to pursue quality improvement through the Six Sigma approach. The Six Sigma approach is in line with Google’s business model for it is aimed at enhancing business success through giving customers pleasant experiences achieved through products of high quality.
Chartered Quality Institute, “What is quality” CQI , 2011. Web.
CNNmoney, “100 best companies to work for”, Cable News Network, 2011. Web.
Darkwah, Kwaku. “SWOT analysis of Google”, Adesua Global , 2011. Web.
Duke University Medical Center, “What is quality Improvement”, Duke University Medical Center. Web.
Graeme Knowles, Six sigma (Ventus Publishing ApS, 2011) International organization for standardization, “Principle 1: Customer focus ”, ISO , 2011. Web.
International organization for standardization, “Principle 2: Leadership ”, ISO , 2011. Web.
International organization for standardization, “Principle 3: Involvement of people ”, ISO , 2011. Web.
International organization for standardization, “Principle 4: Process approach ”, ISO , 2011. Web.
International organization for standardization, “Principle 5: System approach to management ”, ISO , 2011. Web.
International organization for standardization, “Principle 6: Continual improvement”, ISO , 2011. Web.
International organization for standardization, “Principle 7: Factual approach to decision making”, 2011. Web.
International organization for standardization, “Principle 8: Mutual beneficial supplier relationships, ISO , 2011. Web.
International organization for standardization, “Quality management principles”, ISO , 2011. Web.
Investopedia, “ SWOT analysis ”, Investopedia ULC, 2011. Web.
John Gamble and Arthur Thompson, Essentials of Strategic Management: The quest for competitive advantage (Boston: McGraw Hill, 2009), 14.
Norris, Simon “Google’s performance in 2010”, Periscopix Ltd, 2011. Web.
Rex Black, Managing the testing process: practical tools and techniques for managing hardware and software testing . (Canada: Wiley Publishing, Inc., 2002)
Rose Kenneth, Project quality management: why, what and how. (Florida: Rose Publishing, 2005)
Wikiswot, “Google SWOT analysis”, Wiki swot, 2011. Web.
- Impact of the Cultural Attributes on Management in Muslims
- Healthcare Facility Knowledge Management Solutions
- The History and Growth of Google
- How Google Governs the Internet
- Google's view on the future of business
- Difference between Leadership and Management
- An impossibility of objectivity in the world of humans
- Lean and agile operations
- Decision Making as an Essential Process of an Organization
- Decision-Making in Management
- Chicago (A-D)
- Chicago (N-B)
IvyPanda. (2019, May 15). Quality management. https://ivypanda.com/essays/quality-management-essay/
"Quality management." IvyPanda , 15 May 2019, ivypanda.com/essays/quality-management-essay/.
IvyPanda . (2019) 'Quality management'. 15 May.
IvyPanda . 2019. "Quality management." May 15, 2019. https://ivypanda.com/essays/quality-management-essay/.
1. IvyPanda . "Quality management." May 15, 2019. https://ivypanda.com/essays/quality-management-essay/.
IvyPanda . "Quality management." May 15, 2019. https://ivypanda.com/essays/quality-management-essay/.
- To find inspiration for your paper and overcome writer’s block
- As a source of information (ensure proper referencing)
- As a template for you assignment
IvyPanda uses cookies and similar technologies to enhance your experience, enabling functionalities such as:
- Basic site functions
- Ensuring secure, safe transactions
- Secure account login
- Remembering account, browser, and regional preferences
- Remembering privacy and security settings
- Analyzing site traffic and usage
- Personalized search, content, and recommendations
- Displaying relevant, targeted ads on and off IvyPanda
Please refer to IvyPanda's Cookies Policy and Privacy Policy for detailed information.
Certain technologies we use are essential for critical functions such as security and site integrity, account authentication, security and privacy preferences, internal site usage and maintenance data, and ensuring the site operates correctly for browsing and transactions.
Cookies and similar technologies are used to enhance your experience by:
- Remembering general and regional preferences
- Personalizing content, search, recommendations, and offers
Some functions, such as personalized recommendations, account preferences, or localization, may not work correctly without these technologies. For more details, please refer to IvyPanda's Cookies Policy .
To enable personalized advertising (such as interest-based ads), we may share your data with our marketing and advertising partners using cookies and other technologies. These partners may have their own information collected about you. Turning off the personalized advertising setting won't stop you from seeing IvyPanda ads, but it may make the ads you see less relevant or more repetitive.
Personalized advertising may be considered a "sale" or "sharing" of the information under California and other state privacy laws, and you may have the right to opt out. Turning off personalized advertising allows you to exercise your right to opt out. Learn more in IvyPanda's Cookies Policy and Privacy Policy .
Creating a Culture of Quality
by Ashwin Srinivasan and Bryan Kurey
In most industries, quality has never mattered more. New technologies have empowered customers to seek out and compare an endless array of products from around the globe. Shoppers can click to find objective data compiled by experts at organizations such as Consumer Reports and J.D. Power and go online to read user-generated reviews at sites such as Amazon; together, these sources provide an early warning system that alerts the public to quality problems. And when customers are unhappy with a product or service, they can use social media to broadcast their displeasure. In surveys, 26% of consumers say they have used social media to air grievances about a company and its products. And this issue isn’t limited to the consumer space—75% of B2B customers say they rely on word of mouth, including social media, when making purchase decisions.
Partner Center
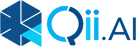
- Book a Demo
Quality Control: Why Is It So Important Now?
By Xinbo Zhang - Apr 17, 2018
5 MIN READ
Providing quality products or services is crucial for all businesses. Whether you are a small, medium or large enterprise, consistent quality products are a great way of maintaining customer satisfaction as well as loyalty. This also means that there are fewer risks to the customers and reduced costs of replacing or repairing failed products.
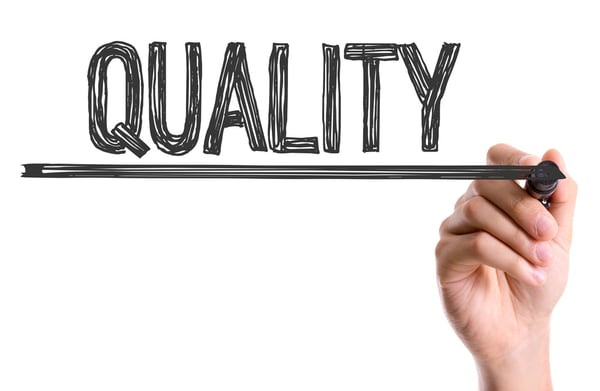
A business that provides quality builds trust, good reputation, and recognition by customers as well as regulatory bodies. Other than loyal repeat customers, the good products enable the organization to gain more clients through referrals, meaning that they spend less on advertising their services.
Quality control goes beyond actual products and services. Because for a business to offer these, its work processes must be well organized, coordinated and executed efficiently. By integrating quality control in the management and work processes, the organization is able to get the maximum productivity at reasonable cost and time.

Quality control in oil and gas industry
In a competitive and capital-intensive industry like the oil and gas, quality control is critical. Besides providing reliable products, it also improves efficiency, safety, and the company’s social responsibility. Without controls, the collapsing infrastructure or failure to observe strict safety practices can cause fires, leakages and other oil-related problems that lead to loss of money for the company, as well as damage to the environment. Further, failures due to lack of maintenance or negligence can lead to loss of life, serious injuries or health implications.
The oil industry operates under complex operational and market conditions. As such, the companies must offer their customers value for money while still making profits. Without good management and controls, it is very hard for any company to stay afloat. They will provide poor services, hence loose customers, or sell their products at higher prices than their production costs, thus make losses. But employing some proven methods can save them operational costs, reduce downtimes, increase efficiency and revenue. Because the company relies on a wide variety of equipment and infrastructure, maintaining them is a major requirement for their success.
A failure in any oil and gas equipment can lead to length downtimes and losses. For this reason, the best approach is to avoid unplanned downtimes by monitoring and inspecting the infrastructure as well as performing regular maintenance. Using modern technologies such as drones inspections , AI, robots and analytics, the oil and gas company can reduce the inspection and maintenance times and costs significantly.
What constitutes quality?
No business, regardless of size, should neglect quality control. However, this should not just focus on the end product; it must address the management, processes, and interaction with customers or suppliers. When well done, it ensures better operations, maintenance of equipment and facilities hence reduced downtimes and losses. This eliminates distrust and fears about safety risks within and outside the company.
For a business to provide quality products, it must embrace have good practices in its management, internal processes, and production areas. This should encourage teamwork, professional development, and integrity.
To produce high-quality products, organizations must pay attention to the all materials, components, structures, and systems that it is using in the manufacturing process. This should also involve the people so that they work as a team towards achieving the best. In particular, all departments must coordinate with each other to ensure smooth flow of operations, fewer downtimes and time to produce a product or deliver service without compromising quality.
The main components of a quality control are:
· Continuous improvement, hence the organization must budget for this and avail resources and time as well as have the drive and determination to achieve the best
· Improving business critical areas all the times, but also not forget the other supporting areas.
· Cooperation and teamwork by managers, supervisors and other staff at all levels
· Ability to listen and respond to customer needs
· Good planning and actions based on findings and feedback from regulatory bodies, customers, and within the organization
· Goal to provide the best quality product or service
· Verify that products comply with operational, safety and other regulatory standards. This helps organizations to rectify any issues such as changing the design before releasing them to the market.

A good quality control approach is to test products as a user and see if there are any flaws or areas that require improvements. Failure to do this, the customers will tell you in a not so polite way. For example, instead of complaining, they will simply walk away and look for alternative products from competitors.
Benefits of quality control
Each organization should, therefore, have a strategy to improve the quality of work processes, performance, and products.
This has a positive effect on employees’ morale and productivity and several benefits and highlighted below.
Meeting the customer need and expectations
A business that implements good quality controls in its processes is in a better position to provide products that fully meet their client’s requirements. This improves customer satisfaction and the potential for the business to retain and have repeat customers over long periods. It also guarantees better and long-term revenues and profits. Failure to address customer expectations will most likely see your present and potential customer looking for alternative products. With a quality product, a business can charge a premium without losing customers, since most of them will not mind the cost as long as you address their needs.
Ensuring compliance with Industry Standards
Quality control is important in ensuring products comply with the standards, especially in the more regulated industries. If making components or subsystems of a certain product, you must meet the quality standards that a lead manufacturer imposes. In such a case, the manufacturers don’t have to inspect or test the components from third part sub-contractors or suppliers as long as they meet an established or recognized standard.
Compliance is also important for the company since it can market its products anywhere in the market as long as they recognize that standard. In addition, it ensures safety and reliability. When your product meets certain standards, they can earn accreditations from various regulatory bodies. This recognition of quality can help an organization to acquire new customers since they will have faith and trust in the products.
Maintain a good reputation
Quality is one of the reasons that companies earn a good reputation. Satisfied customers are likely to talk positive things about a company as well as recommend its quality products to others. In addition, the internet now allows people to share their experiences in social media or review sites. When customers see value in the products and services, their positive reviews can go a long way in enhancing the company’s marketing efforts.
This cannot be said for poor quality products which will definitely attract negative reviews and feedbacks hence damaging the company’s reputation. This can even lead to losses, bad media attention, and possible product recall or even lawsuits.
Good quality is a result of efficient and proper processes. Once the business establishes efficient control systems, it ensures better products and reduced costs. Verifying product quality is one of the main components of quality control which organizations can do in-house and eliminate incidences of product recalls since they can rectify issues before going to the market.
Better cost control
Lack of quality control within the organization as well as coordination across various departments is a recipe for inefficiencies, downtimes and low revenues. Inefficiency increases production costs and could potentially result in poor services and products. A company ends up spending more money to analyze and rectify non-compliant products and may also suffer from recalls since they have to incur additional costs compensating the customers. Finally, producing non-compliant goods exposes the company to possible legal costs.
With quality control, a company is able to plan and budget well hence control the operational and production costs.
Gaining confidence as a company
A company with good quality control practices is usually proud to talk about its products. They have the confidence that all is well and do not fear customers coming up with lawsuits due to malfunctions or accidents arising from defective products.
It also makes employees and investors proud of being associated with the success of the company. In addition, it motivates everyone such that they are able to provide their best and ensure that the company keeps on improving and succeeding.
Share this post

Xinbo Zhang
Xinbo is a digital marketer who is passionate about data, SEO, and inbound marketing.
Related Articles
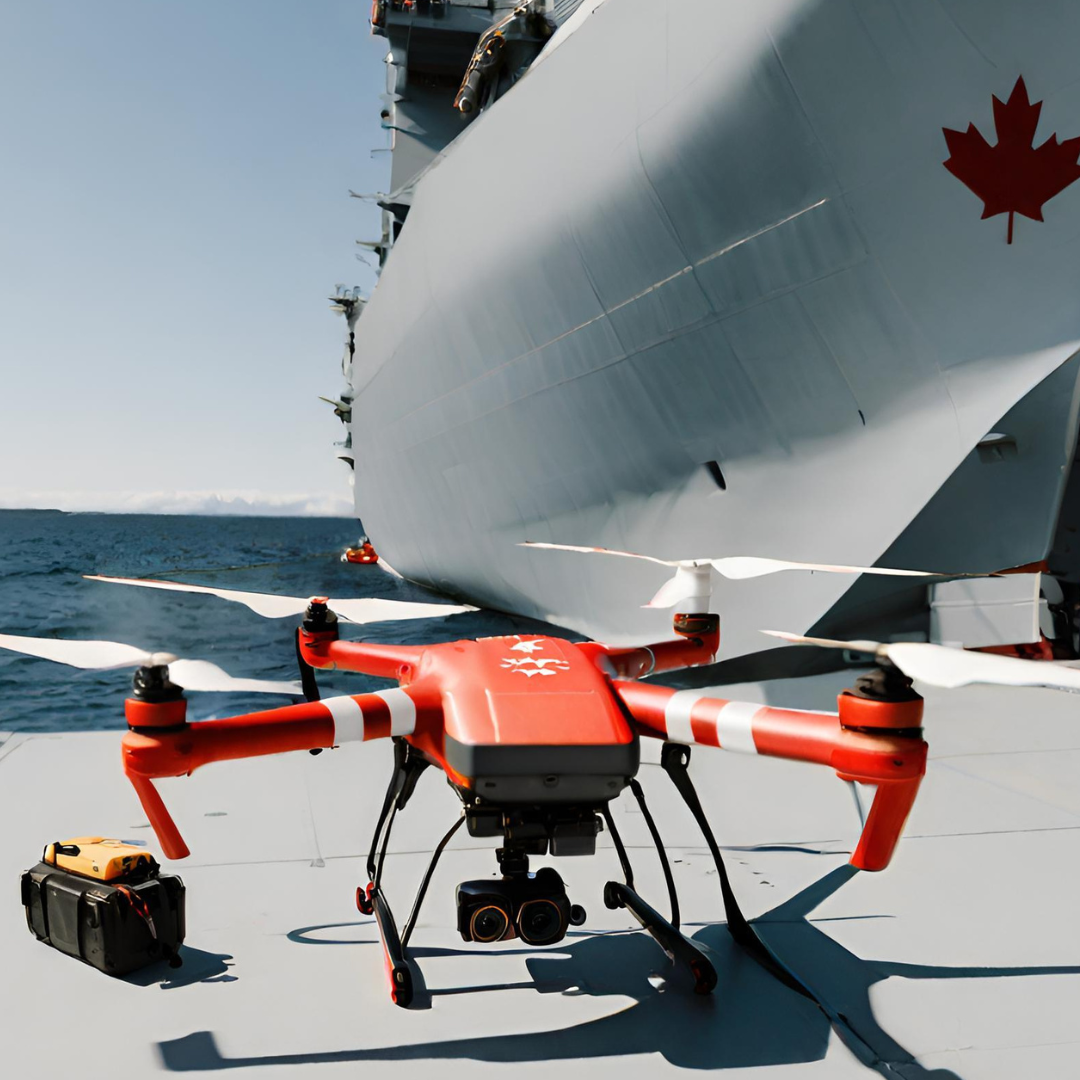
The Evolution of Drone Technology: From Recreation to Critical Inspections
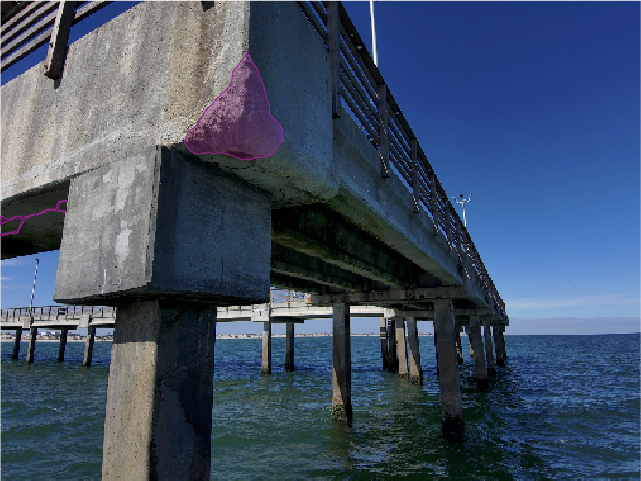
Drone Inspection Overhead Piping Structures and Bridges
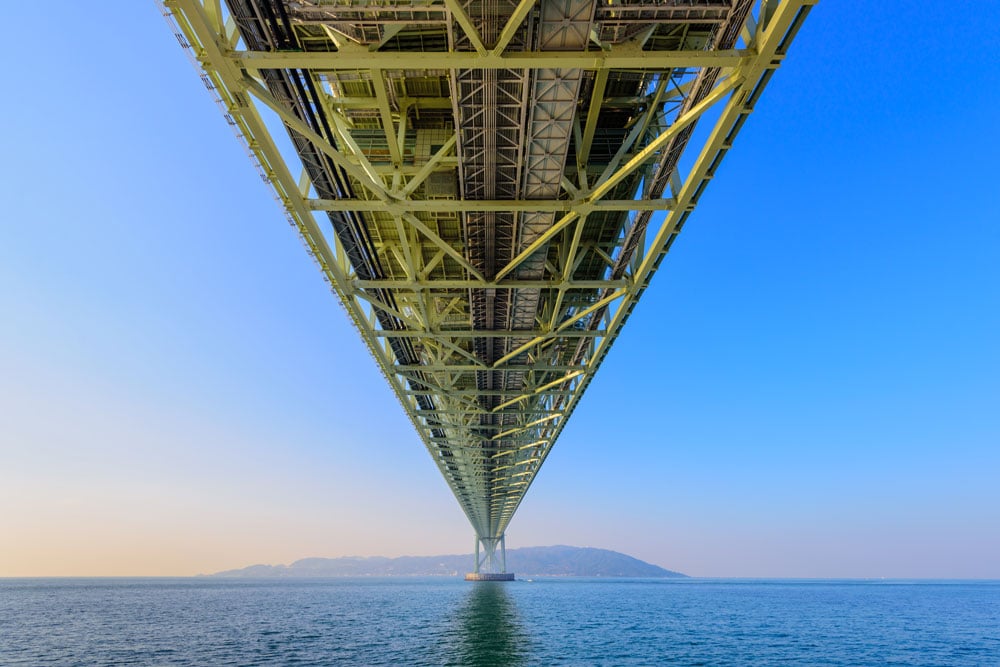
5 Benefits of Using a Drone for Bridge Inspections
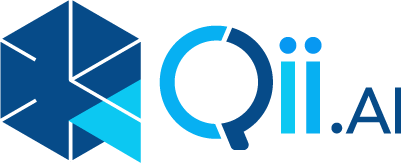
We’re a dedicated Team passionate about creating artificial intelligence, visual analytics, and digital twin technology. Our goal is to deliver real information, increasing asset predictability and employee safety, while reducing time and effort.

Email: [email protected]
© 2024 Qii.AI . All Rights Reserved
Your Article Library
Essay on quality control (with diagram)| products.
ADVERTISEMENTS:
Read this article to learn about Quality Control. After reading this article you will learn about:- 1. Definition of Quality Control 2. Objectives of Quality Control 3. Principles 4. Functions 5. Phases 6. Advantages.
- Essay on the Advantages of Quality Control
Essay # 1. Definition of Quality Control :
According to Alford and Beatly quality control is that “Industrial management technique or group of techniques by means of which products of uniform acceptable quality are manufactured.”
So quality control determines what, when and how much to inspect and what steps should be taken so that defectives are not produced i.e. it is concerned with making things right rather than discovering and rejecting those made wrong. Thus it is preventive and not a corrective action.
Quality control may be defined as “the systematic control of those variables encountered in a manufacturing process which affect the excellence of the product.” Such variables may result from the application of 5 Ms i.e. Men, Machines, Materials, Manufacturing techniques and Money required for acquiring these four inputs.
According to Norman Gaither contrary to popular perception, quality control does not start after the items/goods/products are produced. Rather, it begins much before the goods and services are delivered to consumers. As shown in Fig. 9.1 at the initiation of production system, raw materials, components parts and other inputs must be of acceptable quality before they are allowed to be utilized.
Materials must possess the requisite specifications such as weight, strength surface finish, chemical contents and other characteristics.
Further as the inputs of the production system advance through production processes, the quality of these partly finished items is monitored to identify whether the system is operating on the expected lines. Thus monitoring is essential for operating managers to take corrective action before poor quality products and services are produced.

Hence finished products and services are inspected to determine their acceptability.
In other words it may be defined as that function or collection of various duties which must be performed throughout the organization in order that products are made to measure upto specifications determined from consumers demands or achieve its quality objective or other way round quality is every body’s business and not only of inspection personnel.
Essay # 2. Objectives of Quality Control :
The fundamental purpose of quality control is to maintain the quality standard of the manufactured items/products at optimum cost.
However, some important quality control objectives are as follows:
(1) To decide about the standards of quality that are readily acceptable to the customer/consumer and economical to achieve and maintain.
(2) To carefully observe and analyse the extent of quality deviation in product/part/component from the predetermined standards of quality of the product during manufacture and to determine the causes of such deviation, when it cannot be attributed to chance causes.
(3) To apply corrective measures to achieve the real goal of quality control.
(4) To avoid as far as possible items reaching the customer which are of lower quality standard than considered acceptable.
(5) To take different measures to improve the product quality or checking the quality from dropping below the designed level during manufacture.
Essay # 3. Principles of Quality Control:
The principles of quality control which govern the manufacturing system are as follows:
(1) Under the present competitive manufacturing conditions quality of the goods being manufactured is a variable having upward trend.
(2) The quality control increases the sales volume and decreases the cost of production, distribution and hence makes mass production economical.
(3) The conformance of finished products to the pre-decided standards and specifications should be accomplished by using preventive measures instead of following corrective ones.
Essay # 4. Functions of Quality Control Department :
The quality control department in the organization is represented by its head may be quality controller or quality control engineer. He has to perform following functions:
(1) Advises the organization/management about inspection and quality control policy formulation/or modification.
(2) Decides inspection standards in the light of design tolerances.
(3) Drafts the departmental budget and controls the operating expenses.
(4) Supervises the departmental activities.
(5) Participates as advisor in the top management meetings concerning the production distribution and marketing of the product.
(6) Selects inspection points required for achieving the desired quality levels.
(7) Selects inspection gauges, tools and equipment’s, also ensures that these are maintained in good working conditions.
(8) Collaborates with sampling regarding the choice of statistical quality control techniques/charts to be adopted.
(9) Decides whether sampling inspection or 100% inspection to be adopted for achieving decided quality levels.
(10) Collaborates with statisticians on designing the efficient sampling plans for quality control purposes.
Essay # 5. Phases of Quality Control :
In the words of A.Y. Fegorbaum, “Quality control is an effective system for integrating the quality development, quantity maintenance and quality improvement efforts of the various groups in an organization, so as to enable production of goods and services at the most economical levels which allow full customer satisfaction.”
Thus quality control system consists of the following phases:
Policy of the Organization towards Quality Control of Their Products:
Such policy is generally formulated by the top management of the company as it is dependent upon inter-related factors. The characteristics of the product like price, durability, dependability, appearance and size are the determining factors of quality standards. So the main consideration is the attitude of the product market for the different levels of the quality of product.
Quality and Product Design :
The quality standards provide guidance to designers while suggesting or prescribing the nature of raw materials, manufacturing techniques and other service requirements in order to produce the items/goods of desired standards. Thus standards provide basis for quality control.
In process Quality Control or Quality Control during Manufacturing Cycle:
The following are important stages where quality control techniques can be applied during the course of manufacturing process.
(i) Input materials inspection stage i.e., in coming raw materials/semi-finished/finished parts or components are inspected.
(ii) Product inspection during manufacturing and control/rectification of the process, if needed.
(iii) Inspection and control of the final product.
Thus the quality control techniques try to screen out those products which do not conform to quality standards and suggest corrective action required. Sometimes quality control studies suggest necessity of revision of quality standards or design changes in the product.
Control in Distribution, Installation During and After Sales Use:
The real user of the product is the customer and he should feel satisfied with the performance of the product. So quality control function should be active even after distribution, installation and post-sales use of the product in order to generate the confidence of the consumer in the product.
Essay # 6. Advantages of Quality Control:
The advantages of quality control are listed below:
(1) Quality control may lead to quality improvement of the product which in turn increases sales volume.
(2) It reduces the inspection cost.
(3) Quality control reduces scrap, rejections and rework, thus reducing wastage. So the cost of manufacturing is reduced.
(4) Good quality of the product improves reputation of the enterprise.
(5) Leads to manufacturer and consumer relations improvement.
(6) Results in improvement of technical knowledge and collection of engineering data for process development and manufacturing design thus leading to cost reduction and product standardization.
Related Articles:
- Essay on Inspection of Products | Industries
- Steps for Applying for Quality Control Mechanism
Essay , Industry , Products , Industrial Engineering , Quality Control
Comments are closed.

IMAGES
VIDEO
COMMENTS
Quality control (QC) plays a critical role in ensuring that your company consistently meets customer expectations and regulatory requirements. This comprehensive guide will explore the importance of quality control, its benefits, and key strategies, with industry examples to illustrate its practical applications.
To help you get started, here are 113 quality control essay topic ideas and examples: The importance of quality control in manufacturing. How quality control can improve customer satisfaction. The role of quality control in ensuring product safety. The impact of quality control on a company's reputation.
Looking for a good essay, research or speech topic on Quality Control? Check our list of 67 interesting Quality Control title ideas to write about!
Quality management spans from creating a design and lifecycle plan for a product or service to its production and distribution. The activity involves identifying and measuring process elements, doing performance analysis and applying continuous quality improvements on the products, services and systems of production and distribution.
Quality control is a proactive measure to identify and rectify defects early in production. By catching issues before mass production, businesses can minimize the need for costly rework or...
Creating a Culture of Quality. by. Ashwin Srinivasan. and. Bryan Kurey. From the Magazine (April 2014) In most industries, quality has never mattered more. New technologies have empowered...
A business that provides quality builds trust, good reputation, and recognition by customers as well as regulatory bodies. Other than loyal repeat customers, the good products enable the organization to gain more clients through referrals, meaning that they spend less on advertising their services.
ARMAND V. FEIGENBAUM proposed the theory of total quality control. He believed that high quality could be achieved only through organizational support. He also asserted that the quality must be priority and not afterthought. He emphasised on the administrative viewpoint and considered human issue as a basic issue to quality control.
By the analysis of quality management, the purpose is to address three questions: ISO9000 Quality System’s contribute to a business or organization’s success; the ISO framework’s practice in automotive industry; comment on the benefits and problems in the Six sigma quality management’s future application.
Contents: Essay on the Definition of Quality Control. Essay on the Objectives of Quality Control. Essay on the Principles of Quality Control. Essay on the Functions of Quality Control. Essay on the Phases of Quality Control. Essay on the Advantages of Quality Control. Essay # 1.