Quality – Quality management in construction


Quality management in construction
What is quality management in construction.
Construction projects span a number of functions across a number of specialty parties and trades, but the one thing they all share in common is their desire to deliver quality work - on time and on budget.
Quality management is a key pillar of overall construction project management, and is often the difference between company's success and failure.
Quality management in construction is the policies, processes and procedures put in place (typically by management) to improve an organisation's ability to deliver quality to its customers - whether those customers are clients/owners, contractors or subcontractors - on a consistent and constantly improving basis.
While every construction company on earth wants to deliver quality on every phase of works and every project, it is the establishing of these internal and external principles and guidelines which actually results in quality.
The major objectives of quality management are:
- To minimise the defects on asset delivery or handover
- To identify and solve defects and issues before your customers do - safeguarding your reputation
Achieving these objectives carries some many obvious benefits - none more beneficial than continuing to get more work and building a strong positive reputation.
Creating a quality management plan for construction projects
Preventing mistakes is much more time and cost effective than correcting them - which is why establishing a strong quality management plan is a good way to improve quality. The upfront investment of creating a coherent and comprehensive quality management plan often pays big dividends throughout the life of a project.
Outlined in your quality plan will be four (4) main sections which establish your:
- Quality policies
- Quality objectives (clear and measurable)
- Requirement standards (ISO accreditations etc.)
- Other statutory and legal requirements
As you can see, a quality management plan is both an internal and external tool for construction companies. It ensures that you are adhering to and meeting the necessary quality standards to do work legally and feasibly - and that you are structuring your internal quality control policies and objectives in a way that enables that continuous improvement and ultimately good performance.
Establishing quality procedures
Once a quality plan is established and your 'goal posts' are set, the next obvious phase of quality management is to create procedures which enable you to achieve your objectives.
This phase of quality management design is often more troublesome for companies, as the quality management starts to involve more moving pieces i.e it's easier to sit down and plan than it is to create processes for tens or hundreds of people who then need to be trained and monitored etc.
In saying this, there are four (4) key areas of process focus which when tackled individually or through a comprehensive quality management system or software come together to form this critical process alignment. These key areas are:
- Control of documents and records
- Internal quality audits
- Control of non-conformances
- CAPA (corrective and preventative actions)
As you can see, these quality procedures form a stack through the way that your work moves - from site capture (documents and records) through to corrective and preventative actions (actioning what is captured on site).
Quality management forms and documentation
The quality management process typically starts with those quality management documents - which tend to be plan oriented and comprehensive in nature - outlining and summarising quality management at a high level.
Great quality management process on projects focuses more on how quality is captured, organised and tracked from point where quality matters most - on site.
There are tens or hundreds of quality management forms ranging from simple quality punch lists , hold points and witness points, ITP's (inspection and test plans) and specialty quality forms like welding quality control checklists.
These forms are deployed to engineers, project managers and other workers to ensure that quality is being met - and to inform management or other people where quality has not been met, so that it can be fixed and actioned by the necessary party.
Some companies and teams manage these forms and documentation with paper-based forms, word docs and PDFs, while others use digital forms which enable greater quality standardisation, control and insight.
Outside of these forms and documents - photos, videos and other records are also essential to ensuring quality records are up to scratch for any eventuality including audits.
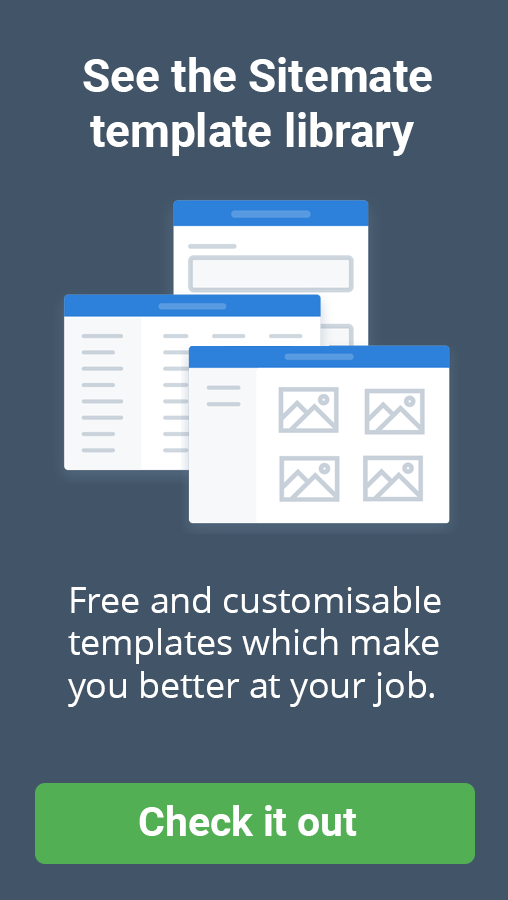
See the Sitemate free quality template library.
Quality assurance vs. quality control.
Quality assurance (QA) and quality control (QC) both sit within the broader category of quality management in construction, but they do have different roles and outputs than one another.
At a high level, quality assurance covers activities from design, development, production and installation and is designed to ensure your customers 'know' your work will be quality; while quality control is more focused on monitoring the actual quality of finished products through objective measurements and numbers.
Both quality assurance and quality control form critical elements of quality management. Without quality assurance, it's hard to build confident working relationships with other parties who rely on your quality assurance and quality plans to make decisions about whether or not to work with you. And without quality control, it's hard to understand how you are tracking in terms of quality - and impossible to make data driven decisions about what needs to be improved.
You also need this quality control data to feed into your quality assurance plans and objectives in order to facilitate the feedback loop and enable improvement.
The different levels of quality control you need
it helps to break quality management down into a couple of layers. It makes it more digestible and more manageable for management and individual project teams.
For management, the level of quality management which must be focused on is organisational level quality control.
The keys to organisational quality control are derived from the levers you have at an organisation level - your processes and procedures, and your resources. You'll want to oversee the systematic implementation of systems and tools which can be rolled out across projects and teams, and you'll want to resource appropriately as well as train and manage appropriately to ensure that projects and activities have what they need in terms of human and other capital to get the job done within the quality standards set.
The next level done is project level quality management, which is usually handled by a combination of management level personnel as well as project level workers including project managers who understand how quality is being assured and delivered in the field.
At this layer, quality assurance concerns and tools are established to make sure that project level information and insights are being captured, organised and tracked properly - and then sent to the right places so that the company and project managers understand what's happening and can make good decisions which result in good projects.
And finally, we have the team and technical layer of quality management. At this level, teams and companies are concerned with the actual output of work and how people, equipment and tools are being used to ensure that the jobs being done are being performed within the acceptable limits.
We stated that this article had all you need to know about quality management, but this is obviously not true. Quality management is a big and broad topic and spans across accreditations, individual tactics and more.
We have plenty more quality information available, but more than that, we have plenty of quality management resources, documents, forms and software tools you can use to improve how you manage and deliver quality every day. Check them out on this 'site'.
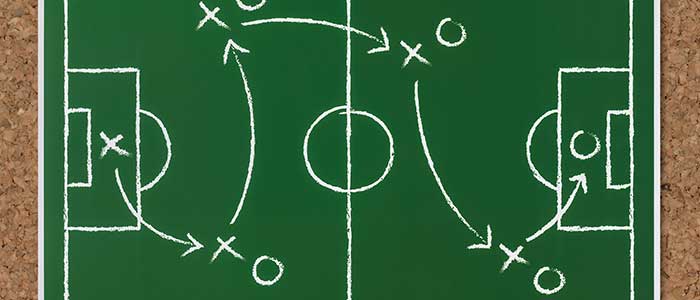
Construction Quality Control Plan template
See the template →
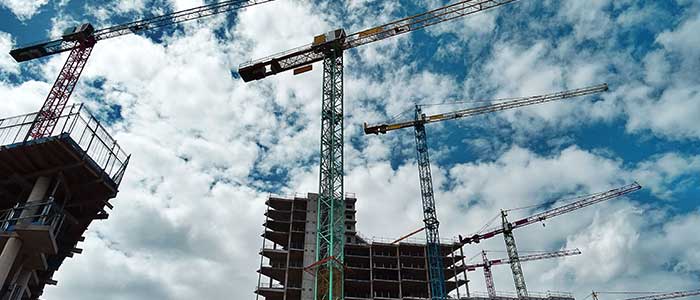
Quality Assurance Plan for Construction
People in 70+ countries use this quality management system to improve the quality and outcomes of their work.
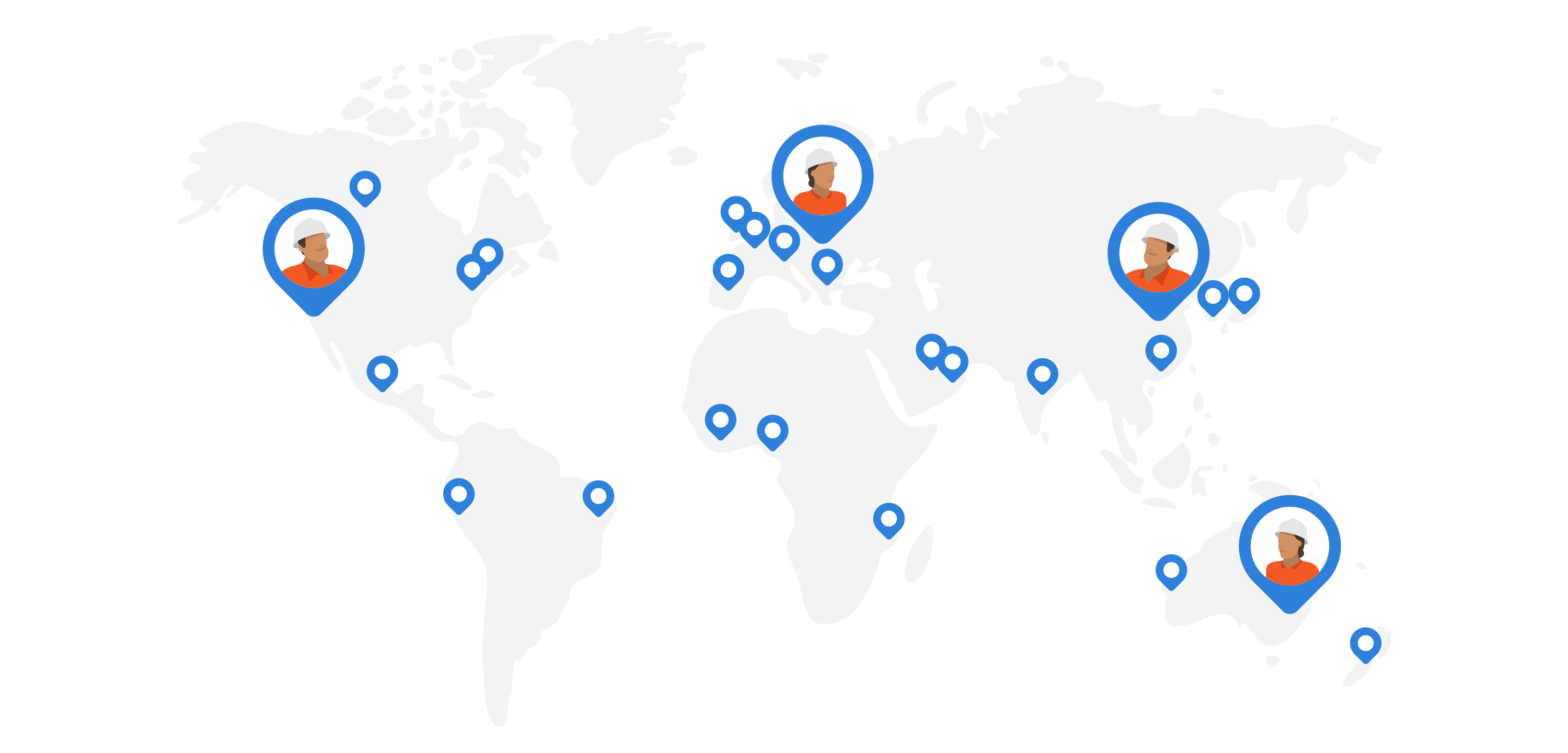
See how you can easily streamline your systems and processes with Sitemate today
About Lance Hodgson
Lance is VP of Marketing at Sitemate. His aim is to bring awareness to a brighter future for the Built World where industrial workers and companies work smarter.
Leave a Comment Cancel Reply
Save my name, email, and website in this browser for the next time I comment.

Quality issues related to the design and construction stage of a project in the Indian construction industry
Frontiers in Engineering and Built Environment
ISSN : 2634-2499
Article publication date: 2 September 2021
Issue publication date: 2 December 2021
Quality in the construction industry is an important issue yet ignored during the initial stages of the life cycle of a project, that is, the design and construction stage. The contribution of stakeholders, especially the architects is generally suspended though it has huge significance in terms of cost and time related to quality. This research endeavors to examine the issues related to the design and construction stages of the project from architects' purview, to understand the relative importance of these issues in the Indian construction industry.
Design/methodology/approach
The study of qualitative data conducted formed a basis for online quantitative data collection that was further analyzed with the help of cross-tabulation and multiple correspondence analysis methods.
The study concludes that the budget of a project is a corresponding factor related to quality concern for architects. The study also established that the quality issues corresponding to high budgets are closely related to the construction stage and are identified as preparation of checklist, and bidding process of hiring the contractor on the lowest bid.
Research limitations/implications
The study is limited to analyzing the perspective of architects; however, other stakeholders of the construction industry may represent a different opinion.
Practical implications
This research emphasizes the importance of the client's role, and need for integration and coordination among stakeholders in the construction industry for effective quality control and management.
Originality/value
The research presents an exhaustive literature review on quality issues and its importance with respect to cost implications, standard practices, sustainability and the life cycle of the project.
- Stakeholder
- Integration
- Total quality management
- Coordination
Khan, S. , Saquib, M. and Hussain, A. (2021), "Quality issues related to the design and construction stage of a project in the Indian construction industry", Frontiers in Engineering and Built Environment , Vol. 1 No. 2, pp. 188-202. https://doi.org/10.1108/FEBE-05-2021-0024
Emerald Publishing Limited
Copyright © 2021, Sharmin Khan, Mohammad Saquib and Anwar Hussain
Published in Frontiers in Engineering and Built Environment . Published by Emerald Publishing Limited. This article is published under the Creative Commons Attribution (CC BY 4.0) licence. Anyone may reproduce, distribute, translate and create derivative works of this article (for both commercial and non-commercial purposes), subject to full attribution to the original publication and authors. The full terms of this licence may be seen at http://creativecommons.org/licences/by/4.0/legalcode
Introduction
Total quality management (TQM) is defined as “ … the integration of all functions and processes within an organization to achieve continuous improvement of the quality of goods and services for customer satisfaction” ( Vincent and Joel, 1995 ). After a long affiliation with the manufacturing business, quality has only recently been applied to the construction industry ( Anetoh et al. , 2013 ). TQM adoption in the construction sector is difficult, according to Hoonakker et al. (2010) , because of the temporary nature of projects, the lack of standardization, the multiple parties involved and the conservative attitude of the construction business. Researchers have approved of a significant influence ( Jimoh et al. , 2019 ) of TQM on the performance of an organization. Asim et al. (2013) emphasized that the quality assurance is the most important indicator of an organization's inclination for quality. According to Chandra (2016) , the traditional organizational structure lacks the ability to integrate functional teams below the top management, as well as the ability to enable effective communication, coordination and control. Also, the complexities of project management have multiplied as the number of stakeholders in building projects has expanded.
Historically the architect was a master builder and administered the project, but the stakeholder management is essential in the current scenario [because the stakeholders are defined by Freeman (1984) as those groups and individuals who can affect or are affected by the achievement of an organization's purpose, and were later established as, “those groups who are vital to the survival and success of the corporation” ( Freeman and McVea, 2001 )]. The functioning, aims, growth and survival of an organization can affect and are influenced by stakeholders ( Chinyio and Olomolaiye, 2010 ). They may have a direct (owners and users of facilities, project managers, facilities managers, designers, shareholders, legal authorities, staff, subcontractors, suppliers, process and service providers) or indirect (rivals, banks, insurance firms, media, community leaders, neighbors, public, government, tourists, consumers and regional development organizations) relationship with the project ( Smith and Love, 2004 ). Akadiri et al. (2012) stressed upon the timely participation of all stakeholders in decision-making as one of the principles in support of sustainability issues, as well as consideration of all sustainable construction principles at every stage of a project's development.
Construction projects of poor quality occur worldwide ( Ali and Wen, 2011 ) leading to serious issues of quality.
Modern architecture is dynamic and versatile owing to the interweaving of virtual spaces and the inclusion of advanced information technology in projects ( Rochegova and Barchugova, 2016 ), and hence the role of the architect has gained crucial importance. Therefore, this research aims to examine the importance of various issues related to quality during the life cycle of a building project from the architects' perspective.
Literature review
The nature of the construction industry is different from manufacturing although both aim at delivering the finished product to customer satisfaction. Oztas et al. (2007) argued that the length of time required to complete construction projects; the development of human relationships; and the difficulty in identifying quality standards, processing input and implementing continuous improvement principles complicate the direct transition of continuous improvement principles from manufacturing to construction. Thus, cost and time have an important role to play as these are decisive areas having a significant impact on the consistency of the final product. However, Willer et al. (2015) observed that many certified organizations' management methods appear to be at variance with the established and fundamental objectives of ISO (International Organization for Standardization). Aside from that, the rise for environmental concerns and the necessity for sustainable construction have promoted the demand for quality in construction projects. Therefore, a thorough investigation is essential to understand the impact of quality issues with respect to cost implications, standard practices and sustainability during the life cycle of the project.
Relationship of quality issues with cost and time
A quality management system must be maintained, evaluated, monitored and enhanced regularly. Construction projects necessitate higher quality at a lower cost and in a shorter time frame making it difficult to achieve a balance between the quality-cost-time relationship. The contractors are under pressure to deliver the project for the best value of money. For a successful project, the three essential parameters of time, cost and quality must be considered together since they are the three points of a triangle, and ignoring one of these variables would have a corresponding impact on the other two ( Hughes and Williams, 1991 ). TQM is said to be focused on continuous improvement, and measurement of quality cost is believed to be a tool for its implementation. To achieve these goals, quality must be related to cost ( Abdelsalam and Gad, 2009 ). To effectively collect and report quality cost data, the level of knowledge of the site workers should be as relevant as that of the management. As a result, there is a strong demand for low-cost training to improve the awareness and skills of site workers. The need for a quality cost structure stems from the fact that cost of quality's consequences cannot be realized without reorganization ( HassenAl-Tmeemy et al. , 2012 ).
Relationship of quality issues with ISO 9000
Pheng and Omar (1997) identified problems related to the maintenance of ISO 9000 as (1) noncommitment and support from top management as they may resist innovation and change, (2) nonavailability of resources, (3) lack of training and education about quality management systems, (4) lack of documentation, (5) poor performance of suppliers and subcontractors, (6) engineering and construction problems, (7) coordination and communication problems.
Further, Pheng and Yeo (1998) explained that implementing ISO 9000 quality control systems will eliminate errors or defects by implementing more prevention steps and supporting them with sufficient appraisal tools to ensure that no defects are delivered to the next step of work or the customer, lowering rectification costs. The engagement of top management is the most significant factor in the effective implementation of ISO 9000.

Relationship of quality issues with sustainability
Buildings utilize more than 30% of energy, consume 40% of resources, produce 40% of waste and 35% of dangerous greenhouse gases ( Tathagat and Dod, 2015 ). The term “sustainability” can be understood in three ways: social, economic and environmental, all of which must be balanced ( Klarin, 2018 ). The environmental goals include improving environmental quality, reducing residues, utilizing less building materials, reusing building materials, recycling wastewater and reducing emissions. Resource conservation, cost efficiency and design for human adaptation are the three objectives identified to form the framework for implementation of sustainable building design and construction based on previously recognized principles of sustainability, that is, social, environmental and economic ( Akadiri et al. , 2012 ). Reduce, reuse, recycle, protect nature, eliminate pollutants, life cycle costing and quality are the guiding concepts ( Kibert, 2016 ). Embodied energy has become more important as it can account for up to 30% of total life cycle energy consumption ( Kamath et al. , 2019 ). However, the education of building operators and occupants is critical to the successful implementation of sustainable techniques in operation and maintenance services ( Miller et al. , 2018 ).
Relationship of quality issues with the life cycle of the project
Abdelsalam and Gad (2009) state that a building's life cycle is divided into four stages: design, construction, post-occupancy or maintenance, and demolition. Further, Ashokkumar (2014) categorized different stages of the project as conceptual planning, feasibility research, design, procurement, construction, acceptance, operation and maintenance. Design and construction (D&C) are two critical identified stages having a considerable impact on the quality of construction projects' outcomes. Kamath et al. (2019) also argue that the concept and design are the bases of any construction project, as the concept stage has the greatest influence in terms of financial consequences and performance, and the design approach has potential to minimize the building's overall environmental impact throughout its life cycle.
The tendency of the client to award the work to the contractor with the lowest bid is one of the causes of defects because of lower quality ( Karim et al. , 2006 ). Michell et al. (2007) reported that in South Africa, approximately 70% of clients chose the traditional approach as the most used procurement scheme. Only 21% of management-oriented programs are documented where client time, cost and quality goals are achieved, whereas the design and build are accounting for just 9%. The importance of project management systems for effective quality, cost and time management is yet to prove its significance in the construction industry. According to Kwakye (2013) , the continued expansion of the design and build (integrated) method as an alternative procurement method to the traditional method is due to a new paradigm change from the fragmented method to the integrated system, as well as the belief that design and construction should be integrated. Chandra (2016) explains that the traditional form of organization is not suitable; firstly, because it lacks in means of integrating different departments below the top management, and secondly it lacks in the facilitation of effective communication, coordination and control.
The integration of D&C practices is essential to create a high-quality structure. Michell et al. (2007) also suggested three different drivers for effective project quality management, including project team integration, emphasis on customer needs and a continuous improvement mechanism. Integrative activities either complement or improve the probability of achieving the core elements of successful teamwork ( Baiden and Price, 2011 ).
The three most important factors related to the coordination of the construction projects are the scheduling, quality assurance plan and all parties' participation in design ( Alaloul et al. , 2016 ). Decisions made during the design stage have a significant impact on its following stages for delivering a high-quality design. The design offices are currently suffering from lack of coordination across various documents and lack of effective frameworks to address such a complicated issue. Contradictions, mismatches, mistakes and inconsistencies in drawings are examples of design synchronization issues that lead to late adjustments later ( Zaneldin, 2016 ).
Planning and supervision, experience, quality of products supplied, management and communication, formal controlling methods, specific roles and responsibilities, and a quality department for overall management are the most frequently preferred factors to control quality ( Wawak et al. , 2020 ). Pheng and Yeo (1998) modified the definition earlier given by Quinn for the quality costs insisting that it consists of three components: preventive costs (to minimize, remove and avoid defects), evaluation costs and failure costs (to detect errors and evaluate the quality of the work done). According to Hasan et al. (2016) , the most effective strategies for controlling defects in construction projects are enhanced workmanship, recognized responsibility for stakeholders, group meetings, good quality building materials, modern construction methods, legible drawings, conformance with specifications and regular inspection on-site. Khan (2021) identified the most common causes of building defects as dampness/seepage, poor craftsmanship, lack of quality control, inappropriate service installation and lack of maintenance during the post-occupancy stage. According to Olagunju et al. (2013) , building collapse is caused by bad design, construction flaws, poor material quality/method of construction, foundation failure, fire tragedy, natural phenomena and inadequate maintenance.
Egemen and Mohamed (2006) found that the expectations of clients are much more than quality and are focused on finishing the project on time within budget. Construction projects consist of activities that involve uncertainty, inherent risks and constraints. Client–contractor collaboration within activities is required for satisfactory project outcomes that have different expectations and needs, and therefore, it is difficult to find complete matching ( Lau and Rowlinson, 2009 ).
Mane and Patil (2015) state that the quality of workmanship in all construction activities is a quality control measure. Following this is the establishment of a quality control laboratory on-site, the maintenance of a construction series and formats, the assignment of duties and responsibilities, site review meetings, sampling and checking, definite quality control procedures, adhering to specified curing and de-shuttering schedules, and coordination. Checklists are considered a powerful tool when used in combination with a routine schedule for quality control. Poor planning is a roadblock in project teams' ability to deliver high-quality results.
Forcada et al. (2012) analyzed that the omission of an aspect of the job, bad finishing or appearance and unsuitable finishing, lead to the most common defects. Lack of quality control is related to defects that occur in buildings during the construction and post-occupancy phase. Fernandez et al. (2016) discussed the defects in two categories: apparent defects [occurring soon after the property is handed over as specified by Forcada et al. (2012) ] and latent defects (during an indefinite period after the handover of the building), and generally require a high cost for repair. Watt (1999) suggests certain factors which are responsible for defects in buildings as the use of improper material, wrong decisions, number of subcontractors, lack of repair works. In certain countries, quality control programs are often combined with protection and environmental systems ( Giacomello, 2014 ) because of which they might not retain their significance.
Research orientation and methodology
This study used a mixed-methodologies approach, which involves gathering, analyzing, and combining quantitative and qualitative research and methods to examine the research problem ( Creswell, 2012 ). The research question explored were as follows: “What are the quality issues related to D&C stages? “What is the perspective of architects toward the quality issues during the D&C stage? and “What is the relationship between an architect's profile and their perception?” Possible indicators of an architect's profile and quality issues were investigated to address the research question. The research aimed to identify the quality issues related to the D&C stage of a building project and the response of architects toward these issues in order to identify the trend in the construction industry, as well as the areas for future concern that need to be focused on. Hence, the objectives of the study can be enlisted as follows: (1) identification of quality issues related to building projects, (2) analysis of identified quality issues with respect to D&C stages, and (3) investigation of the relationship between the architect's profile and identified quality issues.
Literature review and telephonic interviews were conducted to identify and summarize D&C-related quality issues of construction projects with the help of purposive sampling using a structured open-ended questionnaire. Ten architects practicing in Delhi and National Capital Region, having 20+ years of experience in projects of different nature and budgets, agreed to participate.
The quality issues identified were project management schedules, priority for saving cost, late introduction of contractor and consultants, hiring of a contractor on lowest bid, wrong/hasty decisions, unrealistic expectations of the client, omission of an element/task, construction control administration checklist, lack of communication, and noncompliance of quality management plans. The four indicators of the architect's profile are work experience, the nature of the projects undertaken, the budget of projects and the nature of jobs (practicing, academicians or working in both capacities).
There is a significant relationship between the typology of buildings and quality issues.
There is a significant relationship between the years of experience and quality issues.
There is a significant relationship between the budget of projects and quality issues.
There is a significant relationship between the profession and quality issues.
Data collection
An online questionnaire survey was conducted to analyze objective 2 and to investigate the proposed hypotheses for objective 3. In a nonprobability sampling method, voluntary response sampling was conducted by sharing the link to the online questionnaire survey with 200 architects in India, out of which a sample size of 124 volunteered to respond. The response rate was 62% which is acceptable (receiving 20–30%) ( Akintoye, 2000 ) concerning the construction industry. The sampling method ensured that only those architects who had strong opinion on the issue would respond which ensured the reliability of the sample.
Instrument design
A closed-ended questionnaire was designed to obtain the architect's profile and their responses toward quality issues in the D&C stages that consisted of two parts. “Part A” aimed to document the profile of respondents through a set of closed-ended questions with a single choice. “Part B” comprised statements on quality issues with closed-ended options having a multiple choice for inquiring whether the issue is related to design, construction or both stages. In a measure of the internal consistency and reliability of the responses to the questionnaire, Cronbach's alpha ( α ) for ten parameters reporting architect's perception on quality issues was 0.67 which is a moderate and acceptable score, as alpha reaching 0.70 is considered as an adequate measure of reliability or internal consistency in science education despite its limitations ( Taber, 2018 ).
Data analysis and results
A descriptive analysis of the data was performed to obtain frequencies and cross-tabulation of data from the responses. Additionally, the data were analyzed for its statistical significance by performing a chi-square test and later multiple correspondence analysis (MCA), using Statistical Package for Social Sciences SPSS v 23.0. The descriptive analysis for ‘Part A' was conducted for the four indicators of an architect's profile as shown in Table 1 .
The analysis of responses to the ten items on quality issues in three different categories is shown in Figure 1 .
The majority quality issues reported in the design stage were unrealistic expectations of the client followed by the priority for saving the cost; in the construction stage were construction control administration checklist, hiring of the contractor on lowest bid, and noncompliance of quality management plans; and in both stages were wrong/hasty decisions and lack of communication. Figure 2 demonstrates a radar chart for three stages against ten variables of identified quality issues. This graphical representation of multivariate data helps in understanding the quality issues’ proximity with different stages.
Further, a statistical investigation was undertaken to examine the significance of the relationship between the architect's profile and quality issues in the D&C stages. The hypotheses were tested for statistical significance by applying a chi-square test to confirm the association between two categorical variables if there exists a significant chi-square value ( Khangar and Kamalja, 2017 ).
No significant relationship was found between the architect's perception toward quality issues and the typology of buildings χ 2 (8, N = 115) = 9.02, p = 0.341; experience χ 2 (8, N = 115) = 13.86, p = 0.085; and professional experience χ 2 (4, N = 115) = 1.2, p = 0.878.
However, a significant relationship exists between the budget of the project and perception toward quality issues χ 2 (8, N = 115) = 32.04, p < 0.001. The chi-square value is greater than the chi-square critical value, that is, 20.09 ( Bajpai, 2020 ) suggesting that the alternate hypothesis H3 is accepted with 99% level of confidence.
The chi-square test results, therefore, conclude that there is a significant relationship between the budget of projects and quality issues of D&C stages, as perceived by the respondents ( Figure 3 ). Hence hypothesis H3 is accepted, whereas hypotheses H1 , H2 and H4 are rejected.
A supplementary cross-tabulation was conducted to further explore the relationship between the budget and the perception ( Table 2 ). Results revealed that maximum responses were received for projects above 5 crores budget ( n = 718), and most responses pointed toward quality issues in the construction stage of the project ( n = 538).
An MCA model is used to explore and visualize the patterns of relationships among the technology foresight methods and the evaluation criteria in the quantitative phase of research ( Husson and Josse, 2014 ). MCA was performed to examine the significance of the relationship between the budget and quality issues ( Figure 4 ). In MCA, the proportion of inertia accounted for 78.6% in the first dimension, and 21.4% in the second dimension; hence, a two-dimension matrix was analyzed. The inertia can be interpreted as variance in statistics and a stronger model fit is represented by a higher inertia score. The singular value displays the relative contribution of each dimension to an explanation of the inertia, and the values can be interpreted as the association between the rows and columns of the contingency table ( Khangar and Kamalja, 2017 ). The first and second dimensions presented respective singular values of 0.153 and 0.080, and inertia of 0.024 and 0.006.
MCA locates all the groups in the Euclidean space, where the first two dimensions are plotted to investigate the relationships between them. The combined graphical representation provides dual displays with identical row and column geometries, making it easier to identify different relationships ( Ayele et al. , 2014 ). The MCA plot for symmetrical normalization of budget and project stages confirmed the significance of the relationship between the budget of above 5 crores and quality issues in the construction stage of the project, as shown by the proximity of both parameters in the plot ( Figure 4 ). However, lower budget projects relate quality issues to design, but no significant relationship can be identified.
To investigate deeper, a cross-tabulation was conducted to explore the relationship between the budget of the projects and their responses toward ten items in the construction stage only. Most responses reported for quality issues in the construction stage were for the checklist prepared ( n = 57), followed by the hiring of the contractor on lowest bid ( n = 49). The lowest responses were received for unrealistic expectations of the client ( n = 12), wrong/hasty decisions ( n = 17) and lack of communication between the team members ( n = 19).
The qualitative analysis identified ten quality issues related to the D&C stages of the project life cycle, which were then assessed using a quantitative survey to determine how architects perceived the issues. The unrealistic expectations of the client ( Egemen and Mohamed, 2006 ; Michell et al. , 2007 ; Lau and Rowlinson, 2009 ), cost-saving approach ( Watt, 1999 ), late introduction of contractor and consultants ( Michell et al. , 2007 ; Baiden and Price, 2011 ; Kwakye, 2013 ; Mane and Patil, 2015 ; Chandra, 2016 ; Alaloul et al. , 2016 ; Zaneldin, 2016 ), lack of communication ( Baiden and Price, 2011 ; Mane and Patil, 2015 ; Zaneldin, 2016 ; Hasan et al. , 2016 ; Wawak et al. , 2020 ), wrong/hasty decisions ( Watt, 1999 ) and hiring of the contractor on the lowest bid ( Karim et al. , 2006 ; Michell et al. , 2007 ) are highly related to the quality of the project during the design stage. Majority of architects perceived that the quality concern is mostly related to the construction stage of a project and is subjected to issues like controlling the administration of the project formally through a checklist ( Zaneldin, 2016 ), hiring of the contractor on the lowest bid, noncompliance with quality management plans ( Pheng and Yeo, 1998 ; Abdelsalam and Gad, 2009 ; Hassen Al-baidmy et al. , 2012 ; Mane and Patil, 2015 ; Alaloul et al. , 2016 ; Zaneldin, 2016 ; Hasan et al. , 2016 ; Wawak et al. , 2020 ; Khan, 2021 ), omission of tasks ( Forcada et al. , 2012 ; Zaneldin, 2016 ), project management schedules ( Mane and Patil, 2015 ; Alaloul et al. , 2016 ; Wawak et al. , 2020 ), and late introduction of the contractor and consultants. The responses for both stages prioritize wrong/hasty decisions and lack of communication as important quality issues. The results are in confirmation with Prajapati et al. (2015) that it is difficult to expect high-quality service if only the lowest tender is accepted, so a beneficial paradigm shift from “lowest price wins” to “multicriteria selection” for contractor selection is required. The results also emphasize the need to consider together the three parameters time, cost, and quality for a successful project as emphasized by Hughes and Williams (1991) .
On further investigation regarding the relationship between the architect's profile and quality issues during the D&C stage, it was observed that budget has a significant relationship with the quality issues. The majority of the quality issues are related to the construction stage, as the budget of the project increases. Besides this, quality issues related to design were reported as relatively less significant including issues such as communication between designer and team members implying that the role of communication is not significantly realized during all stages of the project significantly. Habibi et al. (2019) identified that lack of communication and slow decision-making processes are performance indicators, which are highly affected by managerial approaches. The responses for projects according to different budgets are 30–50 lakh ( n = 46), 51 lakh–1.5 crore ( n = 42), 1.6–2.5 crore ( n = 41), 2.6–5.0 crore ( n = 37) and above 5 crore ( n = 345). The highest responses were received from respondents for projects of budget above 5 crores. It is observed that the four most important and vital quality concerns that had a lower response rate are under the client's domain. It has been emphasized by researchers ( Stojcetovic et al. , 2014 ) that top quality demands higher cost and time, but the practice of reducing the cost and time essential for the implementation of the project affects quality. Unfortunately, the observed quality issues are unrealized although many researchers have stressed upon the importance of the design process and early participation of construction experts in construction projects ( Kania et al. , 2020 ).
Research implications and limitations
The endeavor of this research is to sensitize the stakeholder's participation during different stages of the project's life cycle, especially D&C. The Construction Industry Institute (CII) has promoted the concept of constructability focused on “the optimum use of construction knowledge and experience in planning, engineering, procurement and field operations to achieve overall project objectives” ( CII, 1986 ). The objective of all construction projects is to accomplish the quality project within estimated time and budget, but the issues such as delay in the integration of team, wrong/hasty decisions, lack of communication related to D&C having a significant impact on the quality of the project are neglected. Besides this, the client's unreasonable expectations and desire to save money affect the project's quality. There is a need to emphasize upon quality issues during all stages of the project, and architects can play a key role by the integration of the team and laying emphasis on various quality issues since the inception of the design idea. According to studies, 70–85% of building maintenance and running costs can be controlled during the design stage, that accounts for a significant amount of total building life cycle costs ( Krstic and Marenjak, 2012 ), though it is practically possible only with the consent and awareness of the client; hence, the responsibility of the architect is proliferated, as the involvement of internal stakeholders is to be promoted. There is a dire need to focus on issues of integration of the team at an early stage of the project and coordination among the stakeholders because issues like hiring contractors at a later stage in the project and lack of communication are related to the late integration of the team. Regular review meetings and checklists are key drivers for controlling the quality. It is also noteworthy that the design decisions have an impact on quality, and the risk factors can be minimized with the integration of the team at the initial stage of the project. Thus the research proposes certain guidelines for stakeholders of the construction industry, such as, (1) comply with quality management plans, (2) practice early integration of the team and regular communication, (3) prepare project schedules, (4) hire contractor on expertise basis, (5) notify client about future cost implications due to unrealistic expectations, (6) avoid hasty decision-making without discussion and (7) organize regular review meetings for evaluation of prepared checklists. The research presents the architect's perspective regarding issues related to quality during the D&C stages of the project in the Indian construction industry, and emphasizes the need for integration and teamwork to effectively handle quality issues. However, the opinion of other stakeholders in the construction industry may differ from the results of this study and can be examined through similar studies in different contexts.
The research focused on ten quality issues related to D&C during the life cycle of the project. The first objective was achieved by identifying quality issues in the construction industry through interviews from experts and literature survey. The quality issues were identified as project management schedules, priority for saving cost, late introduction of contractor and consultants, hiring of the contractor on lowest bid, wrong/hasty decisions, unrealistic expectations of the client, omission of an element/task, construction control administration checklist, lack of communication and noncompliance of quality management plans. The second objective was fulfilled by analyzing the quality issues through a quantitative survey. The results highlight that high concerns of quality issues in the design stage of the project are unrealistic expectations of the client, priority for saving the cost, late introduction of the contractor and consultants, and lack of communication between team members. Major quality issues reported in the construction stage were not preparing and following the construction control administration checklist, hiring of the contractor on the lowest bid, and noncompliance of quality management plans. The common quality issues simultaneously reported in both stages by the respondents were wrong/hasty decisions and lack of proper communication between team members.
The third objective of the research focusing on the descriptive and inferential analysis confirms the significance of the relationship between the budget and quality issues in the construction stage of the project. This may suggest that the higher cost of the project enforces the inclusion of project management systems, and quality control issues are implemented with concern. On the contrary, the typology of the project, experience and the nature of the profession are not significantly related to quality issues. Cross-tabulation of the budget of projects and responses to quality issues within the construction stage provided further insights into key issues that need attention, and may help to positively address the quality concerns during project management. This study highlights the crucial role of the architect in controlling the quality issues, which have a substantial impact on the life cycle of a project. Successful implementation of management plans in consultation with team members during the initial stages of the project can address the growing concern for environmental issues and the need for sustainable construction.
Quality issues in different stages
Radar chart for D&C stages
Hypothetical framework
MCA plot for budget and project stages
Profile of the respondents
Note(s): L-lakh, Cr-crore, n -frequency, NA-not applicable
Abdelsalam , H.M.E. and Gad , M.M. ( 2009 ), “ Cost of quality in Dubai: an analytical case study of residential construction projects ”, International Journal of Project Management , Vol. 27 No. 5 , pp. 501 - 511 , doi: 10.1016/j.ijproman.2008.07.006 .
Akadiri , P.O. , Chinyio , E.A. and Olomolaiye , P.O. ( 2012 ), “ Design of a sustainable building: a conceptual framework for implementing sustainability in the building sector ”, Buildings , Vol. 2 , pp. 126 - 152 , doi: 10.3390/buildings2020126 .
Akintoye , A. ( 2000 ), “ Analysis of factors influencing project cost ”, Construction Management and Economics , Vol. 18 No. 1 , pp. 77 - 89 , doi: 10.1080/014461900370979 .
Alaoul , W.S. , Liew , M.S. and Zawawi , N.A.W.A. ( 2016 ), “ Identification of coordination factors affecting building projects performance ”, Alexandria Engineering Journal , Vol. 55 No. 3 , pp. 2689 - 2698 , doi: 10.1016/j.aej.2016.06.010 .
Ali , A.S. and Wen , K.H. ( 2011 ), “ Building defects: possible solutions for poor construction workmanship ”, Journal of Building Performance , Vol. 2 No. 1 , pp. 59 - 69 .
Anetoh , J.C. , Ndubisi , E.C. and Nwankwo , C.A. ( 2013 ), “ The emergence of total quality management in the marketing of services in Nigeria ”, Journal of Management and Corporate Governance , Vol. 5 No. 2 , pp. 53 - 66 .
Ashokkumar , D. ( 2014 ), “ Study of quality management in construction industry ”, International Journal Innovative Research in Science Engineering and Technology , Vol. 3 No. 1 , pp. 36 - 43 .
Asim , M. , Zaman , S. and Zarif , T. ( 2013 ), “ Implementation of total quality management in construction industry: a Pakistan perspective ”, Journal of Management and Social Science , Vol. 9 No. 1 , pp. 24 - 39 .
Ayele , D. , Zewotir , T. and Mwambi , H. ( 2014 ), “ Multiple correspondence analysis as a tool for analysis of large health surveys in African settings ”, African Health Sciences , Vol. 14 No. 4 , doi: 10.4314/ahs.v14i4.35 .
Baiden , B.K. and Price , A.D.F. ( 2011 ), “ The effect of integration on project delivery team effectiveness ”, International Journal Project Management , Vol. 29 , pp. 29 - 136 , doi: 10.1016/j.ijproman.2010.01.016 .
Bajpai , N. ( 2020 ), Building Research Methods , Pearson Education India .
Chandra , P. ( 2016 ), Projects: Planning, Analysis, Selection, Financing, Implementation, and Review , 8th ed. , McGraw Hill Education .
Chinyio , E. and Olomolaiye , P. ( 2010 ), “ Introducing stakeholder management ”, in Chinyio , E. and Olomolaiye , P. (Eds), Construction Stakeholder Management , Blackwell Publishing .
Construction Industry Institute (CII) ( 1986 ), Constructability: A Primer , University of Texas , Austin .
Creswell , J.W. ( 2012 ), Educational Research: Planning, Conducting, and Evaluating Quantitative and Qualitative Research , 4th ed. , Pearson Education , Upper Saddle River, NJ .
Egemen , M. and Mohamed , A.N. ( 2006 ), “ Clients' needs, wants and expectations from contractors and approach to the concept of repetitive works in the Northern Cyprus construction market ”, Building and Environment , Vol. 41 No. 5 , pp. 602 - 614 , doi: 10.1016/j.buildenv.2005.02.021 .
Fernandez , J.M.M. , González , C.P. , Cabal , V.A. and Balsera , J.V. ( 2016 ), “ Analysis of the quality control planning in residential construction projects in Spain ”, Journal of Construction , Vol. 15 No. 2 , pp. 106 - 114 , doi: 10.4067/S0718-915X2016000200011 .
Forcada , N. , Macarulla , M. , Fuertes , A. , Casals , M. , Gangolells , M. and Roca , X. ( 2012 ), “ Influence of building type on post-handover defects in housing ”, Journal of Performance of Constructed Facilities , Vol. 26 No. 4 , pp. 433 - 440 , doi: 10.1061/(ASCE)CF.1943-5509.0000225 .
Freeman , R.E. ( 1984 ), Strategic Management: A Stakeholder Approach , Pitman Publishing , Boston .
Freeman , R.E. and McVea , J. ( 2001 ), “ A stakeholder approach to strategic management ”, in Hitt , M. , Freeman , E. and Harrison , J. (Eds), The Blackwell Handbook of Strategic Management , Oxford University Press , Oxford , doi: 10.2139/ssrn.263511 .
Giacomello , H. , Gonzalez , M.A.S. and Kern , A.P. ( 2014 ), “ Implementation of an integrated management system into a small building company ”, Journal of Construction , Vol. 13 No. 3 , pp. 10 - 18 .
Habibi , S.M. , Kermanshachi , S. and Rouhanizadeh , B. ( 2019 ), “ Identifying and measuring engineering, procurement, and construction (EPC) key performance indicators and management ”, Infrastructures , Vol. 4 No. 14 , doi: 10.3390/infrastructures4020014 .
Hasan , M.I.M. , Razak , N.N.A. , Endut , I.R. , Abu Samah , S.A. , Ridzuan , A.R.M. and Saaidin , S. ( 2016 ), “ Minimizing defects in building construction project ”, Jurnal Teknologi , Vol. 78 , pp. 79 - 84 .
HassenAl-Tmeemy , S.M. , Abdul-Rahman , H.A. and Harun , Z. ( 2012 ), “ Contractors' perception of the use of costs of quality system in Malaysian building construction projects ”, International Journal of Project Management , Vol. 30 No. 7 , pp. 827 - 838 , doi: 10.1016/j.ijproman.2011.12.001 .
Hoonakker , P. , Carayon , P. and Loushine , T. ( 2010 ), “ Barrier and benefits of quality management in the construction industry: an empirical study ”, TQM and Business Excellence , Vol. 21 No. 9 , pp. 953 - 969 , doi: 10.1080/14783363.2010.487673 .
Hughes , T. and Williams , T. ( 1991 ), Quality Assurance , BSP Professional Books , Oxford .
Husson , F. and Josse , J. ( 2014 ), “ Multiple correspondence analysis ”, in Greenacre et Blasius (Ed.), The Visualization and Verbalization of Data Chapter: Multiple Correspondence Analysis , CRC .
Jimoh , R. , Oyewobi , L. , Isa , R. and Waziri , I. ( 2019 ), “ Total quality management practices and organizational performance: the mediating roles of strategies for continuous improvement ”, International Journal Construction Management , Vol. 19 No. 2 , pp. 162 - 177 , doi: 10.1080/15623599.2017.1411456 .
Kamath , S. , Kamath , R. , D'Souza , B. , Soman , B. , Raj , A. and Kamath , L. ( 2019 ), “ Green buildings: sustainable construction principles ”, International Journal of Civil Engineering and Technology , Vol. 10 No. 1 , pp. 1882 - 1892 .
Kania , E. , Radziszewska-Zielina , E. and Sladowski , G. ( 2020 ), “ Communication and information flow in polish construction projects ”, Sustainability , Vol. 12 No. 9182 , pp. 1 - 23 , doi: 10.3390/su12219182 .
Karim , K. , Marosszeky , M. and Davis , S. ( 2006 ), “ Managing subcontractor supply chain for quality in construction ”, Engineering, Construction and Architectural Management , Vol. 13 No. 1 , pp. 27 - 42 , doi: 10.1108/09699980610646485 .
Khan , S. , Hussain , A. and Saquib , M. ( 2021 ), Causes of Defects in Buildings and Their Relationship with Life Cycle - Design, Construction, and Post-occupancy Stage , Transactions PACE 2021 , Ataturk University , pp. 469 - 473 .
Khangar , N.J. and Kamalja , K.K. ( 2017 ), “ Multiple correspondence analysis and its applications ”, Electronic Journal of Applied Statistical Analysis , Vol. 10 No. 02 , pp. 432 - 462 , doi: 10.1285/i20705948v10n2p432 .
Kibert , C.J. ( 2016 ), Sustainable Construction: Green Building Design and Delivery , John Wiley & Sons .
Klarin , T. ( 2018 ), “ The concept of sustainable development: from its beginning to the contemporary issues ”, Zagreb International Review of Economics and Business , Vol. 21 No. 1 , pp. 67 - 94 , doi: 10.2478/zireb-2018-0005 .
Krstic , H. and Marenjak , S. ( 2012 ), “ Analysis of buildings operation and maintenance costs ”, Građevinar , Vol. 64 No. 4 , pp. 293 - 303 , doi: 10.14256/JCE.651.2011 .
Kwakye , A. ( 2013 ), Construction Project Administration in Practice , Routledge .
Lau , E. and Rowlinson , S. ( 2009 ), “ The expectations, needs, risks, and constraints for project performance ”, in Dainty , A. (Ed.), 25th Annual ARCOM Conference , Nottingham , pp. 585 - 594 .
Mane , P.P. and Patil , J.R. ( 2015 ), “ Quality management system at construction projects ”, The Civil Engineering PG Conference , MAEER's MIT , India , pp. 323 - 327 .
Michell , K. , Bowen , P. , Cattell , K. , Edward , P. and Pearl , R. ( 2007 ), “ Stakeholder perceptions of contractor time, cost and quality management on building project ”, The CIB World Building Conference on Construction for Development (CIB) , Rotterdam, SA , pp. 231 - 240 .
Miller , W. , Liu , A.L. , Amin , Z. and Gray , M. ( 2018 ), “ Involving occupants in net-zero-energy solar housing retrofits: an Australian sub-tropical case study ”, Solar Energy , Vol. 159 , pp. 390 - 404 .
Olagunju , R. , Aremu , S. and Ogundele , J. ( 2013 ), “ Incessant collapse of buildings in Nigeria: an architect's view ”, Civil and Environmental Research , Vol. 3 No. 4 , pp. 49 - 54 .
Oztas , A. , Guzelsoy , S.S. and Tekinkus , M. ( 2007 ), “ Development of quality matrix to measure the effectiveness of quality management systems in Turkish construction industry ”, Building and Environment , Vol. 42 No. 3 , pp. 1219 - 1228 , doi: 10.1016/j.buildenv.2005.12.017 .
Pheng , L.S. and Omar , H.F. ( 1997 ), “ Integration, segmentalism and the maintenance of quality management systems in the construction industry ”, Building Research and Information , Vol. 25 No. 1 , pp. 36 - 49 , doi: 10.1080/096132197370598 .
Pheng , L.S. and Yeo , H.K.C. ( 1998 ), “ A construction quality costs quantifying system for the building industry ”, International Journal of Quality and Reliability Management , Vol. 15 No. 3 , pp. 329 - 349 , doi: 10.1108/02656719810198926 .
Prajapati , R. , Pitroda , J. and Bhavsar , J.J. ( 2015 ), “ A review on competitive bidding procedure and strategy of bidding ”, Journal of International Academic Research for Multidisciplinary , Vol. 2 No. 12 , pp. 84 - 96 .
Rochegova , N. and Barchugova , E. ( 2016 ), “ Project management methodology of contemporary architecture ”, Procedia Engineering , Vol. 165 , pp. 1911 - 1917 , doi: 10.1016/j.proeng.2016.11.941 .
Smith , J. and Love , P.E.D. ( 2004 ), “ Stakeholder management during project inception: strategic needs analysis ”, Journal Architectural Engineering , Vol. 10 No. 1 , pp. 22 - 33 .
Stojcetovic , B. , Lazarevic , D. , Prlincevic , B. , Stajcic , D. and Miletic , S. ( 2014 ), “ Project management: cost, time, and quality ”, 8th International Quality Conference , Center for Quality, University of Kragujevac , Serbia , pp. 345 - 350 .
Taber , K.S. ( 2018 ), “ The use of Cronbach's alpha when developing and reporting research instruments in science education ”, Research in Science Education , Vol. 48 No. 1 , pp. 1273 - 1296 , doi: 10.1007/s11165-016-9602-2 .
Tathagat , D. and Dod , R.D. ( 2015 ), “ The inception and evolution of EIA and environmental clearance process–laying emphasis on sustainable development and construction ”, International Journal Engineering Research and Applications , Vol. 1 No. 5 , pp. 22 - 28 .
Vincent , K.O. and Joel , E.R. ( 1995 ), Principles of Total Quality , Kogan Page , London .
Watt , D. ( 1999 ), Building Pathology: Introduction and Practice , Blackwell , Oxford .
Wawak , S. , Ljevo , Z. and Vukomanovic , M. ( 2020 ), “ Understanding the key quality factors in construction projects—a systematic literature review ”, Sustainability , Vol. 12 No. 24 , pp. 1 - 25 , doi: 10.3390/su122410376 .
Willer , D. , Coffey , V. and Trigunarsyah , B. ( 2015 ), “ Examining the implementation of ISO 9001 in Indonesian construction companies ”, The TQM Journal , Vol. 27 No. 1 , pp. 94 - 107 , doi: 10.1108/TQM-08-2012-0060 .
Zaneldin , E. ( 2016 ), “ Preventing coordination problems during the design stage of projects ”, IJOER , Vol. 2 No. 9 , pp. 40 - 53 .
Corresponding author
Related articles, we’re listening — tell us what you think, something didn’t work….
Report bugs here
All feedback is valuable
Please share your general feedback
Join us on our journey
Platform update page.
Visit emeraldpublishing.com/platformupdate to discover the latest news and updates
Questions & More Information
Answers to the most commonly asked questions here

Alternative Quality Management Systems for Highway Construction (2015)
Chapter: chapter 4 : case studies of alternative quality management.
Below is the uncorrected machine-read text of this chapter, intended to provide our own search engines and external engines with highly rich, chapter-representative searchable text of each book. Because it is UNCORRECTED material, please consider the following text as a useful but insufficient proxy for the authoritative book pages.
CHAPTER 4 : CASE STUDIES OF ALTERNATIVE QUALITY MANAGEMENT 4.1 Introduction Previous chapters focused on the historic and current state of quality management practice and identified the most common quality management models in use in the highway industry. The focus of this chapter is on the ten case studies conducted by the research team and the relevant analyses and observations of those case studies. Case studies formed the bulk of the original research conducted in Phase I of this research project and offered examples of quality management practices delivered under a variety of project conditions, which may serve as models for the organization of quality management systems for future projects. This chapter begins with a discussion of the protocol and methodology used to conduct the case studies and secure the relevant information from each in a justifiable manner. Included in this section are a breakdown of the case study demographics and an explanation of how the case studies were chosen. Following the section on methodology are truncated versions of the case study summaries. The full case study summaries are presented in the appendices in full detail. A large amount of information is contained in the summaries. In order to assist with comparing among the various studies, tabular summaries of relevant details are presented at the end of the summaries section. The case study summaries include a description of the general trends observed when comparing the case studies. The cross-case analysis produced a list of potential alternative QM system tools. These tools are associated with applicable QAOs, which furnishes a mechanism by which agencies can determine which tools will be more valuable to a given projectâs QM requirements. The tools are discussed in detail in in chapter 5. 4.2 Case Study Protocol While the survey conducted in Task 2 provided some useful insights into the overall state-of-the- practice, the case studies were the primary source of practical applications of innovative quality management techniques in Phase I and for the practices recommended by the guidebook in Phase II. As a result of the central role in the research project, the research team gave serious consideration to how best to conduct the case studies and capture their valuable information. While researchers may differ in their preference for which research techniques and strategies to use in various situations, case studies represent a valuable tool in the arsenal of any researcher. Case studies are particularly useful in answering questions about how things are done in detail, especially when examining a number of different cases (Yin 2003). In this project, the use of the case study method was essential in capturing not only the unique nature and methods of each project but also understanding questions of why projects were conducted a certain way and how successful those methods were. One of the traditional arguments against the use of case studies has been their perceived lack of 87
rigor. Recognizing this common criticism, the authors sought to generate a defensible, repeatable method to guide the case study process. This method was formalized and recorded in the case study protocol for the project, which Appendix C presents in detail. Yin (2003) provided guidance in creating the case study protocol. The case study protocol serves a number of purposes. Primarily it establishes the purpose of the case studies and the questions to be answered by them. While this information was later useful for the case study participants (albeit in a shortened form), clearly stating this information at the start of this crucial document ensured that all researchers who were conducting case study interviews understood the ultimate goals of the research. The background information for the protocol included key sections of the project proposal and work plan like the explicit research objectives and key questions and also included relevant readings which are fundamental to this research. The most important component of the protocol was the information relating to field procedures which are the heart of the case study protocol and form the bulk of the document. These procedures establish a standard method to conduct all of the case studies and seek to generate consistent and comparable results among the case studies. The key pieces of the field procedures are the case study questionnaire and the case study questions. The questionnaire was one of the first documents to be sent participants. While each case study is unique and the interview process sought to capture that uniqueness, the purpose of the questionnaire was generate a standard set of readily comparable information. To that end, the questionnaire was primarily populated with yes/no questions and matrices of checklists and was specified to be filled for every case study in its entirety. The section listing case study questions on the other hand was not expected to be answered in its entirety; instead, these questions were supplementary and to be used at the discretion of the researcher. Many of the questions represented in the questionnaire are open-ended questions crafted to generate in-depth discussion to help fill in the details the surveys cannot easily capture. The field procedures also include sample letters to send as well as a flowchart showing the order of key communications with participants. 4.3 Case Study Process The case study protocol included a minimum of two pilot case studies to evaluate the efficacy of the process before modifying the case study procedures and completing the rest. Rather than conducting the minimum of two, three pilot case studies were conducted to allow each of the three principal research teams an opportunity to become familiar with the case study protocol for this project and provide comments on it or recommendations for changes. One of the key changes, which came out of this, was firmly establishing the order to gather information, as discussed below. The case study protocol for this project included a particular order of communications and interactions with project participants that was to be followed on every project. First, direct contact was made with the project either over the telephone or in person. While initial inquiries occurred via email, personal contact was vital to every case study. The primary importance of personally contacting the key project participants lay in securing a champion for the research 88
effort. Because participants received no compensation for their time by the research team, it was essential to make contact with participants who expressed enthusiasm about assisting with the research effort and was in a position to coordinate with the rest of the participants on the project. After securing the support of a project champion, all of the key project participants (typically Owner/agency, designer, and builder quality or project managers) were sent a copy of the case study questionnaire and asked to complete and return it before the interview. This was the key change from the pilot case studies. Originally, the priority lay in simply completing the questionnaire before the end of the interview process. However, after the first round of case studies, it was discovered that the questionnaire was too time consuming to fill out in an interview setting and limited the amount of open-ended questions and discussion, which are vital to case studies, which could occur. Subsequent case study participants were given explicit instructions to return the questionnaires before the interview. While freeing up time for more expansive questions in the interviews, having multiple participants fill out the questionnaire independently exposed differing opinions, which led to further discussion for clarification in the interviews. After the questionnaires were completed, interviews were conducted with all of the key project staff. While these interviews typically took place with all the participants at once, in some instances, schedule conflicts were too great to overcome and individual interviews were used instead. While interviews were conducted in person as much as possible, due to limited budgets and geographic dispersion of project participants, in several cases interviews were conducted over the phone. When conducted in person, the authors recorded and showed the participantsâ answers using an electronic projector in real time so they could verify the accuracy of the recorded statements. By combining standard questionnaires with personal interviews, the case studies generated the consistent, comparable data and the unique features of each project that were sought. The next step in the case study process was the collection of relevant project documents for later review. When possible, these documents were requested in electronic form for easier reproduction and use, though some materials were provided as hard copies. The documents requested included procurement and prequalification documents and project and quality management plans. The information in the documents was used to answer later questions that arose and to examine specific language used. Finally, once the interview were complete, the information gathered was combined and used to craft the case study reports found in the appendices. When necessary, project participants were contacted after the interview for further clarification, but these contacts were kept to a minimum by the comprehensive nature of the list of case study questions in the field procedures. 4.4 Case Study Selection and Demographics Given the limited number of case studies that were expected as part of this research, the selection of useful case studies was crucial. Guiding the selection process were a number of criteria that each narrowed the number of possible case studies. Table 4-1 contains a description of the selected case study projects. 89
Table 4-1 â List of Case Studies P â Pilot case study The primary criterion for case study selection was that the projects under consideration utilize some form of alternative quality management. While the range of possible alternative quality management procedures leads is long, this one requirement greatly limits the number of potential case studies as most projects still utilize the baseline delivery and quality management methods. Next, case studies were selected such that all the major alternative delivery methods, design- build (DB), construction manager/general contractor (CM/GC), and public-private partnership (PPP), were well represented. A concerted effort was made to seek out projects from agencies that were mature in their experience with alternative delivery methods. Related to this effort was the requirement that the list of case studies include at least two projects from non-STAs and one project that utilized the ISO 9000 certification. Projects from the U.S. Army Corps of Engineers (USACE) and TriMet, a regional transit provider in Oregon, were located and used as case studies. In spite of a reasonable search, an ISO 9000 certified project was not identified. However, the USACE project utilized ISO 9000 certified organizations and QM documents, and the concessionaire for FDOT project used ISO 9000 documentation to train its subcontractors on the projectâs QM system. The next goal in case study selection was achieving at least a moderate level of geographic dispersion. Although the project was not funded to include significant travel to project sites, a conscious effort was made to ensure that no more than two projects came from the same state and that projects were not clustered in a particular portion of the country. Figure 4-1 shows this dispersion. Lastly, while there was no set dollar value requirement for projects, only those projects of at least moderate size and scope were considered as these were more likely to have sophisticated quality management procedures in use. # Agency State Size Delivery Method Project Mode 1 WSDOT Washington $18 million DBB w/eci George Sellar Bridge Bridge 2 ODOT, P Oregon $135 million CMGC Willamette River Bridge Bridge 3 TriMet Oregon $113 million CMGC Portland Transit Mall Transit 4 USACE Kansas $175 million CMGC Tuttle Creek Dam Dam 5 UDOT Utah $730 million CMGC Mountain View Corridor Highway 6 CDOT, P Colorado $29.5 million DB US 160 4th Lane Addition Highway 7 UDOT Utah $135 million DB I-15 Widening-Beck Street Highway 8 MnDOT, P Minnesota $120 million DB Hastings River Bridge Bridge 9 FDOT Florida $1.2 billion PPP I-595 Express Corridor Highway 10 TxDOT Texas $1.5 billion PPP SH130 Turnpike Extension Highway 90
Figure 4-1 â Geographic Dispersion of Case Studies After all the criteria were considered, 10 suitable projects were identified and used as case studies. As mentioned above, one of the most important aspects of all the projects was identification of a champion for the research effort. To that end, personal contacts of the primary investigators were leveraged to provide a more personal connection to each project when possible with the hope of increasing participant interest and involvement. Of the 10 projects identified there are/is: ï§ One DBB project utilizing early contractor involvement in the design process ï§ Two PPP projects ï§ Three DB projects ï§ Four CMGC projects (one of which uses the USACE ECI delivery method) ï§ One dam project ï§ One transit project ï§ Three bridge projects ï§ Five highway projects ï§ Eight states represented ï§ $3.8 billion represented 4.5 Case Study Summaries The following subsections contain brief summaries of each of the ten case studies conducted for this project. Each summary begins with key project data including project name; the name of the agency or owner responsible for the project; the location of the project; the project delivery and procurement methods used; the contract payment type; and a brief description of the nature of the project. The project quality profile provides a quick snapshot of the basic premise of the 91
quality management system used on the project and any notable features of that system. The graphic included with each summary is the QAO diagram for that project. The diagram is a visual representation of who controls which key aspects of design and construction quality management. Further explanation of these diagrams can be found in the full case study reports in the appendices. The section devoted to QM plans describes whether these plans were required for design or construction and if so, what was required to be in them and when they were required to be submitted. The tables devoted to quality management roles list the primary quality management actions taken on most projects during design and construction and list (in greater detail than the QAO diagrams) who was responsible for what tasks. Following these tables is a list of notable and effective quality management procedures used on the project as determined by the authors. 4.5.1 George Sellar Bridge, Washington Project Name: George Sellar Bridge Additional Eastbound Lane Name of Agency: Washington State Department of Transportation (WSDOT) Location: MP 0.16 to MP 0.39 over the Columbia River between the towns of Wenatchee and East Wenatchee in the state of Washington Project Delivery Method/Procurement/Contract Type: DBB/A+B+C bidding/Lump sum Project Description: The primary focus of this project was to add an additional eastbound lane to the George Sellar Bridge in order to substantially increase its capacity. To do so, sidewalks on either side of the roadway were removed and the bridge deck was expanded from 54â to 61â wide using the new space. The new configuration accommodates five 11â wide lanes and a narrow median and shoulders. A 10â wide cantilevered pedestrian and bike pathway was added to the south side of the bridge and a tunnel was constructed through the East side approach to accommodate a new recreational trail. In order to accommodate the new load and increased traffic area the bridge required significant strengthening of 100 truss members and modification of the parabolic portals at either end of the bridge. Project Quality Profile: As a traditional design-bid-build project designed by WSDOT staff, the project quality profile exactly matches the baseline quality system. The constructor performed construction quality control and WSDOT performed all other quality functions. The notable feature of this project was its use of a joint WSDOT/AGC panel early in the design process to inform aspects of the design. QAO: Figure 4-2 shows that the QAO for this project was Deterministic. 92
Project Acceptance Construction Quality Assurance Design Quality Assurance Design Quality Control Construction Quality Control Design Released for Construction Construction Released for Final Payment Quality Assurance Constructorâs Responsibility Designerâs Responsibility Independent Assurance (if reqâd) - functional audit -physical audit WSDOTâs Design Staff Responsiblity WSDOTâs Construction Staff Responsibility Independent Assurance (if reqâd) - functional audit -physical audit Figure 4-2 â George Sellar Bridge QAO QA/QC Plans: While this project did use quality management plans on this project, they were more of a minor addition to the larger and more important project management plans (PMPs). WSDOT emphasizes the use of PMPs as the focus of the planning effort and references relevant documents related to quality as needed. For design, the PMP included references to WSDOTâs standard design quality management plan included in its Bridge Design Manual. As with design, the focus of the construction planning effort was a PMP, not a unique quality management plan. Instead, the primary quality management requirement was that the contractor conforms to the standard specifications of WSDOT and the special provisions for the project. Included in these documents were specific material and testing requirements or references to WSDOTâs materials manual, which lays out acceptable materials and certification tests. The contractor was never required to submit a formal quality control plan. 93
Quality Management Responsibility Allocation: A summary of design and construction QM roles is shown in table 4-2. Table 4-2 â Summary of design and construction QM roles Responsibility allocation for design management tasks Agency Design Staff Agency PM Staff Design Consultant Staff Constructorâs Pre-const. Staff Agency-hired QA/oversight Consultant Other, specify below Technical review of design deliverables â â Checking of design calculations â Checking of quantities â Acceptance of design deliverables â Review of specifications â â Approval of final construction plans & other design documents â Approval of progress payments for design progress N/A N/A N/A N/A N/A N/A Approval of post-award design QM/QA/QC plans N/A N/A N/A N/A N/A N/A Responsibility allocation for construction management tasks Agency Design Staff Agency PM Staff Design Consultant Staff Constructorâs Construction Staff Agency-hired QA/oversight Consultant Other, specify below Technical review of construction shop drawings â â â cursory Technical review of construction material submittals â â â cursory Checking of pay quantities â â Routine construction inspection â Quality control testing â â Verification testing â â Acceptance testing â Approval of progress payments for construction progress â â Approval of construction post- award QM/QA/QC plans â Report of nonconforming work or punchlist. â Effective QM Practices: ï§ Use of a joint AGC and WSDOT panel to inform the design process ï§ Use of pre-bid meetings for clarification 94
4.5.2 Willamette River Bridge, Oregon Project Name: Willamette River Bridge Name of Agency: Oregon Department of Transportation (ODOT) Location: I-5 over the Willamette River in Lane County at the border of the cities of Eugene and Springfield, OR. Project Delivery Method/Procurement/Contract Type: CM/GC/Best-Value/Lump sum w/ GMP Project Description: The primary focus of the Willamette River Bridge project was the construction of two 1800â+ long arch bridges capable of carrying three lanes of traffic. Work included construction of the first bridge, demolition of an existing temporary bridge, and construction of the second bridge. In addition, the project included the repair or replacement of the nearby 100â long Canoe Canal Bridge, realignment and grading work along I-5 to match the new bridges, and construction of sound walls, associated pedestrian trails, and extensive public artwork. The project was conducted above an active railroad corridor, Franklin Blvd, and an exit ramp for Franklin Blvd. Project Quality Profile: All four of the project parties collaborated on the design quality control function because of the contractorâs early involvement in the design process and the presence of Oregon Bridge Delivery Partners (OBDP) a program manager. ODOT provided primary quality assurance functions on the project and was supplemented by OBDP in that role. ODOTâs approach to construction quality control was rather restrictive limiting the contractor to only conduction quality control testing and nothing more. Acceptability, confidence, and verification testing were all performed by ODOT. 95
QAO: Figure 4-3 shows that the QAO for this project was Deterministic. Project Acceptance Construction Quality Assurance Design Quality Assurance Design Quality Control Construction Quality Control Design Released for Construction Construction Released for Final Payment Independent Assurance (if reqâd) - functional audit -physical audit Quality Assurance Constructorâs Responsibility ODOT/OBDPâs CEI Staff Responsibility Designerâs Responsibility ODOT/OBDPâs Design Staff Responsibility Owner Verification (if reqâd) Independent Assurance (if reqâd) - functional audit -physical audit Figure 4-3 â Willamette River Bridge QAO QA/QC Plans: ODOT required the design team to submit a standard quality control plan to be used by the design team and all of its consultants. The plan was submitted for approval as a part of the design teamâs proposal and was evaluated in determining which designer to award the contract to. Conversely, the construction quality control plan wasnât a required submittal until after the CMGC contract was awarded. In addition, the construction quality control plan was significantly less detailed than that required of the design team as the project made use of a construction quality management system identical to that used on ODOT design-bid-build projects. The project team went out of its way to ensure that the project looked and felt like a design-bid-build project on the construction side of things. 96
Quality Management Responsibility Allocation: A summary of design and construction QM roles is shown in table 4-3. Table 4-3 â Summary of design and construction QM roles Responsibility allocation for design management tasks Agency Design Staff Agency PM Staff Design Consultant Staff Constructorâs Pre-const. Staff Agency-hired QA/oversight Consultant Other, specify below Technical review of design deliverables â â Checking of design calculations â Checking of quantities â â â Acceptance of design deliverables â Review of specifications â â â Approval of final construction plans & other design documents â â â Approval of progress payments for design progress â Approval of post-award design QM/QA/QC plans â Responsibility allocation for construction management tasks Agency Design Staff Agency PM Staff Design Consultant Staff Constructorâs Construction Staff Agency-hired QA/oversight Consultant Other, specify below Technical review of construction shop drawings â â Technical review of construction material submittals â â Checking of pay quantities â â Routine construction inspection â OBDP+ ODOT â Quality control testing â Verification testing â Acceptance testing â Approval of progress payments for construction progress â Approval of construction post- award QM/QA/QC plans â Report of nonconforming work or punchlist. â OBDP+ ODOT 97
Effective QM Practices: ï§ Early contractor involvement in the design process ï§ Flexibility afforded by CMGC method ï§ Allowing contractor to use competitive bidding OR negotiated contracts for subcontractors 4.5.3 Portland Transit Mall Revitalization, Oregon Project Name: Portland Transit Mall (Greenline) Revitalization Name of Agency: Tri-County Metropolitan Transportation District or Oregon (TriMet) Location: The Portland Transit Mall is located along SW 5th and 6th Avenues in downtown Portland, OR and stretches 1.4 miles south from Union Station to I-405 Project Delivery Method/Procurement/Contract Type: CM/GC/Best-Value/Cost plus fee w/ GMP Project Description: The focus of this case study was the construction of a new light rail transit line along 5th and 6th Avenues, which was part of a larger revitalization of the whole Portland Transit Mall. The project included substantial utility relocation work both before and during construction of the rail bed, installation of 2.8 miles of light rail track, gantries, and supporting systems (signals, power substations, etc.), and the construction of a triple track turnout loop at the southern extent of the project. In addition, the contract included construction of 12 new light rail stations complete with shelters and signage. Project Quality Profile: All three of the project parties collaborated on the design quality control function as a result of the CMGC delivery method and the contractorâs early involvement in the design process. TriMet provided all primary quality assurance functions on the project and was supplemented with inspection staff from the city of Portland and local utilities. TriMet permitted the contractor to employ its own quality control inspectors and to perform its own materials testing if the staff were nationally certified for the work. Confidence testing was performed at the discretion of TriMetâs resident engineer by 3rd party testing labs kept on-call by TriMet. The project was marked by close collaboration between the contractorâs quality control manager and TriMetâs resident engineer. 98
QAO: Figure 4-4 shows that the QAO for this project was Deterministic. Project Acceptance Construction Quality Assurance Design Quality Assurance Design Quality Control Construction Quality Control Design Released for Construction Construction Released for Final Payment Independent Assurance (if reqâd) - functional audit -physical audit Quality Assurance Constructorâs Responsibility ODOT/OBDPâs CEI Staff Responsibility Designerâs Responsibility ODOT/OBDPâs Design Staff Responsibility Owner Verification (if reqâd) Independent Assurance (if reqâd) - functional audit -physical audit Figure 4-4 â Portland Transit Mall QAO QA/QC Plans: The design QM plans used by TriMet are in some sense standardized across projects and delivery method types. TriMet has a formal quality assurance program approved by the Federal Transit Administration that design quality management plans (for both in-house staff and design consultants) must comply with. The contractor was required to develop a quality control plan and submit it for approval after it was awarded the project, it was not an evaluation criteria in the procurement process. 99
Quality Management Responsibility Allocation: A summary of design and construction QM roles is shown in table 4-4. Table 4-4 â Summary of design and construction QM roles Responsibility allocation for design management tasks Agency Design Staff Agency PM Staff Design Consultant Staff Constructorâs Pre-const. Staff Agency-hired QA/oversight Consultant Other, specify below Technical review of design deliverables N/A â â â Checking of design calculations N/A â â Checking of quantities N/A â â â Acceptance of design deliverables N/A â â Review of specifications N/A â â â Approval of final construction plans & other design documents N/A â â Approval of progress payments for design progress N/A â Approval of post-award design QM/QA/QC plans N/A â Responsibility allocation for construction management tasks Agency Design Staff Agency PM Staff Design Consultant Staff Constructorâs Construction Staff Agency-hired QA/oversight Consultant Other, specify below Technical review of construction shop drawings N/A S P Technical review of construction material submittals N/A P S Checking of pay quantities N/A P Routine construction inspection N/A S P Quality control testing N/A P S Verification testing â Note 1 N/A P P Acceptance testing N/A P Approval of progress payments for construction progress N/A P Approval of construction post- award QM/QA/QC plans N/A P Report of nonconforming work or punchlist. N/A S S P P â Primary responsibility; S â Secondary responsibility 100
Effective QM Practices: ï§ Contractor involvement early in the design process ï§ Electronic recording and submission of daily reports ï§ Allowing contractor utilize own inspectors for QC and materials testing ï§ Use of CMGC delivery method 4.5.4 Tuttle Creek Dam Safety Assurance Project, Kansas Project Name: Tuttle Creek Dam Safety Assurance Project Name of Agency: US Army Corps of Engineers (USACE) Location: Tuttle Creek, north of the City of Manhattan in Kansas, along the Big Blue River Project Delivery Method/Procurement/Contract Type: Corps Early Contractor Involvement (ECI)/Best-Value/Progressive GMP Note: ECI is the terminology used by USACE for a CMGC delivery method. It should not be confused with the ECI delivery method used in Europe and for the remainder of this report will be referred to as a CMGC delivery method. Project Description: The Tuttle Creek Dam Safety Ground Modification Project is the largest Dam Safety, ground modification project on an active Dam that has ever been performed. This project consisted of multiple contracts to make various repairs to the dam. The Ground Modification base contract was awarded in 2005 to Treviicos South for $49M (this was the ECI/CMGC Contract). A contract to provide structural reinforcement and bearing rehabilitation on the 18 Spillway Tainter Gates was awarded in 2007 and completed in 2010 for $10M. The wire ropes for the Tainter Gates will be replaced in 2011 and 2012. Project Quality Profile: The quality management system that was used on this project was not substantially different from that used by other agencies. USACE has documentation outlining the approach to quality assurance and quality procedures on projects. Also, an individual project specific quality management plan was written for the Tuttle Creek Dam project. The construction, design and project management organizations were all ISO certified. 101
QAO: Figure 4-5 shows that the QAO for this project was Deterministic. Project Acceptance Construction Quality Assurance Design Quality Assurance Design Quality Control Construction Quality Control Design Released for Construction Construction Released for Final Payment Quality Assurance Constructorâs Responsibility Designerâs Responsibility Independent Assurance (if reqâd) - functional audit -physical audit Ownerâs Responsibility Ownerâs Responsibility Independent Assurance (if reqâd) - functional audit -physical audit Figure 4-5 â Tuttle Creek Dam Safety Assurance Project QAO Model QA/QC Plans: The design QM plans used on this project were different from design-bid-build (DBB) projects because this was a one of a kind design that involved both an advisory panel of experts as well as allowing for the construction contractor to participate in the design review process to help improve quality. The QM plan was not different as such, but it emphasized how heavily the government intended to rely on the construction contractors input. The construction QM plans used on this project were no different from the QM plans used on traditional DBB construction projects. 102
Quality Management Responsibility Allocation: A summary of design and construction QM roles is shown in table 4-5. Table 4-5 â Summary of design and construction QM roles Responsibility allocation for design management tasks Agency personnel Consultant design staff Constructorâs preconstructi on staff Agency-hired QA/oversight consultant Technical review of design deliverables â â â Checking of design calculations â Checking of quantities â â Acceptance of design deliverables â â â Review of specifications â â â Approval of final construction plans & other design documents â â Approval of progress payments for design progress â Approval of post-award design QM/QA/QC plans â Responsibility allocation for construction management tasks Agency personnel Consultant design staff Constructorâs construction staff Agency-hired QA/oversight consultant Technical review of construction shop drawings â â Technical review of construction material submittals â â Checking of pay quantities â Routine construction inspection â Quality control testing â Verification testing â Acceptance testing â Approval of progress payments for construction progress Approval of construction post-award QM/QA/QC plans Report of nonconforming work or punch list. â Effective QM Practices: The following is a list of effective practices used on USACE projects. ï§ Advisory Panel ï§ Resident Management System (RMS) - An automated system for submittal and document control. ï§ Design check - The designer must have his work checked by highly experienced technical person before each design submittal. This checking procedure is essential to the production of a quality product. ï§ Quality control checklists - Checklists for designers and their checkers to ensure completeness. 103
ï§ Interdisciplinary checks - Interdisciplinary coordination is a key element of the QCP. The checks are usually conducted by the design team members who check each otherâs work to assure compatibility. ï§ District Quality Control (DQC) Review - An internal peer review for quality control. ï§ Agency Technical Review (ATR) - An ATR is an independent technical review, which is a critical examination by a qualified person or technical team outside the submitting district. ï§ Independent External Peer Review (IEPR) - An IEPR is an independent review of the technical efficacy of a decision document by a review organization external to USACE. ï§ Quality management review - Quality management reviews to assure that USACE Regulations are met. 4.5.5 Mountain View Corridor Project, Utah Project Name: Mountain View Corridor (MVC) Project Name of Agency: Utah Department of Transportation (UDOT) Location: The Mountain View Corridor encompasses Salt Lake County west of Bangerter Highway between I-80 and the Utah County border Project Delivery Method/Procurement/Contract Type: CM/GC/Best-Value/GMP Project Description: Initial construction includes building two outside lanes in each direction with signalized intersections where future interchanges will be located. This new roadway requires extensive grading and excavation, relocating utilities, acquiring property, constructing drainage systems, building bridges and structures, and laying new pavement. Trail sections will also be built. Future construction will build out the remainder of the corridor by adding interchanges and more lanes to achieve a fully functional freeway. Project Quality Profile: UDOT will provide some quality control and all quality assurance for the Project. The contractor is responsible for assuring the quality of the work of the subcontractors at all levels. UDOT or its designee will perform limited inspection and testing to audit and verify that all work and materials comply with the drawings, specifications, and all reference standards. Audits will be performed on a systematic basis and will be coordinated with the Quality Control Plan or as warranted by general quality trends. 104
QAO: Figure 4-6 shows that the QAO for this project was Assurance. Project Acceptance Construction Quality Assurance Design Quality Assurance Design Quality Control Construction Quality Control Design Released for Construction Construction Released for Final Payment Independent Assurance (if reqâd) - functional audit -physical audit Owner Verification (if reqâd) Quality Management Independent Assurance (if reqâd) - functional audit -physical audit Designerâs Responsibility Ownerâs Responsibility Constructorâs Responsibility Ownerâs Responsibility Quality Assurance Figure 4-6 â Mountain View Corridor QAO QA/QC Plans: The design QM plans are no different from the QM plans used on traditional design projects. For UDOT the delivery method does not affect the quality methods. The quality methods are driven by the size of the project. The contractor was required to develop, implement, and maintain a Quality Control Plan. The Quality Control Plan had to include, at a minimum, provisions for continued education and training, toolbox meetings, various meetings with subcontractors and suppliers, and other activities. In addition, the Quality Control Plan had to include the Contractor assuring the quality of the work of the subcontractors at all levels. 105
Quality Management Responsibility Allocation: A summary of design and construction QM roles is shown in table 4-6. Table 4-6 â Summary of design and construction QM roles Responsibility allocation for design management tasks Agency personnel Consultant design staff Constructorâs preconstruction staff Agency-hired QA/oversight consultant Technical review of design deliverables â â â Checking of design calculations â Checking of quantities â â Acceptance of design deliverables â Review of specifications â â â Approval of final construction plans & other design documents â Approval of progress payments for design progress â Approval of post-award design QM/QA/QC plans â Responsibility allocation for construction management tasks Agency personnel Consultant design staff Constructorâs construction staff Agency-hired QA/oversight consultant Technical review of construction shop drawings â â Technical review of construction material submittals â â Checking of pay quantities â â Routine construction inspection â â Quality control testing â Verification testing â â Acceptance testing â Approval of progress payments for construction progress â Approval of construction post-award QM/QA/QC plans â â Report of nonconforming work or punch list. â â Effective QM Practices: The following practices are used on the MVC project and lead to enhanced quality: ï§ Project Records File and Distribution System ï§ Regular Project Team Meetings ï§ Reviews - The contractor is required to participate in formal constructability and material availability reviews that are conducted at up to four milestones throughout the Project. ï§ Quality Personnel Education and Training - The extent of training is to correspond with the following: o Scope, complexity, and nature of the activity o Education, experience, and proficiency of the person o Specific requirements of the Contract Documents 106
ï§ Goal-Setting Session - The Contractor was required to participate in an initial goal-setting session with UDOT 4.5.6 U.S. 160 4th Lane Addition, Colorado Project Name: U.S. 160 4th Lane Expansion Name of Agency: Colorado Department of Transportation (CDOT) Location: U.S. 160 at Farmington Hill Interchange/Wilson Gulch in Grandview Colorado just east of Durango, CO Project Delivery Method/Procurement/Contract Type: Modified Design-build (Low bid procurement) Note: Modified DB is a CDOT alteration on standard practice for DB. Modified DB contains a higher level of initial design and is awarded on a low-bid best value basis. For the remainder of this report, this case study will be listed simply as using a DB delivery method. Project Description: The project included the design and construction of four bridges in mountainous terrain and crossing U.S. 160 and the environmentally-sensitive Wilson Gulch. Highly-curved ramp geometries, high settlement soils and a limited construction season created design challenges which were overcome to deliver a successful design. Project Quality Profile: CDOT was responsible for all quality assurance and independent assurance on the project. The design builder was responsible for all quality control, both design and construction. Outside of the design builder having the responsibility for design QC, the project quality management was no different than a design-bid-build project. CDOT does use the same quality management system across all project, regardless of delivery method. CDOT performed testing on all materials; it appears that quality management system for the construction was heavily directed by the agency. The lack of a design builder created construction QC plan is further evidence that the construction quality management was directed by CDOT. 107
QAO: Figure 4-7 shows that the QAO for this project was Oversight. Project Acceptance Construction Quality Assurance Design Quality Assurance Design Quality Control Construction Quality Control Design Released for Construction Construction Released for Final Payment Owner Verification (if reqâd) Quality Assurance Design Builderâs Responsibility Ownerâs Responsibility Figure 4-7 â U.S. 160 4th Lane Addition QAO QA/QC Plans: The primary quality management plan in place for this project was the design quality control plan (DQCP) which was created by the designer on the design-build team. This plan had to be submitted and approved by CDOT before any work could begin. CDOT required a quality control plan to be created by the design builder, but it appears that the DQCP was the document that was what all parties referred to when asked about QA/QC plans for the project. 108
Quality Management Responsibility Allocation: Table 4-7 shows a summary of design and construction QM roles. Table 4-7 â Summary of design and construction QM roles Responsibility allocation for design management tasks Agency personnel Consultant design staff Constructorâs preconstruction staff Agency-hired QA/oversight consultant Technical review of design deliverables â â Checking of design calculations â Checking of quantities â â â Acceptance of design deliverables â Review of specifications â Approval of final construction plans & other design documents â Approval of progress payments for design progress â Approval of post-award design QM/QA/QC plans â Responsibility allocation for construction management tasks Agency personnel Consultant design staff Constructorâs construction staff Agency-hired QA/oversight consultant Technical review of construction shop drawings â â Technical review of construction material submittals â â Checking of pay quantities â Routine construction inspection â Quality control testing â Verification testing â â Acceptance testing â Approval of progress payments for construction progress â Approval of construction post-award QM/QA/QC plans â Report of nonconforming work or punchlist. â Effective QM Practices: Design quality control forms that were included as parts of the appendix of the DQCP were very effective in tracking and organizing the various Design QC processes. 4.5.7 I-15 Widening, Beck Street Project, Utah Project Name: I-15; Widening, 500 North to I-215 Name of Agency: Utah Department of Transportation (UDOT) 109
Location: I-15, 500 North to I-215, Utah Project Delivery Method/Procurement/Contract Type: DB/Best-Value/Lump Sum Project Description: The project consists of the reconstruction of Interstate 15 from 500 North in Salt Lake City to the I-215 overpass in Davis County. The project includes the design, reconstruction, and widening of the mainline highway to include an Express Lane and three general purpose lanes in each direction. The work includes the total reconstruction of Mainline I- 15 between 500 North and the I-215 overpass. UDOT requires removal and replacement of the existing Beck Street Bridge with twin 600-feet, four-span bridges. Additionally, the 1100 North and U.S. 89 bridges will be replaced with two-span rapid bridges. The 800 North Bridge will be removed permanently. Project Quality Profile: The Quality Management plans used on this project were the same as those used on traditional UDOT projects, except the tracking and administration was handled differently. This was because the goals were the same with regards to testing requirements etc. except payment was not by quantity. Lump Sum payment was used; therefore quantities were recorded separately for verification testing. 110
QAO: Figure 4-8 shows that the QAO for this project was Oversight. Project Acceptance Construction Quality Assurance Design Quality Assurance Design Quality Control Construction Quality Control Design Released for Construction Construction Released for Final Payment Independent Assurance (if reqâd) - functional audit -physical audit Owner Verification (if reqâd) Quality Assurance Independent Assurance (if reqâd) - functional audit -physical audit Design- Builderâs Responsibility Ownerâs Responsibility Figure 4-8 â I-15 Widening QAO Model QA/QC Plans: UDOT specified that the Quality Management Plan (QMP) had to include procedures for design-builder construction quality control, design quality control and assurance, and Agency inspection and testing. The Design-Builder had the primary responsibility for the overall quality of the work including the quality of work produced by subcontractors, fabricators, suppliers, and vendors. An IQF was not required for this project. UDOT was to conduct oversight and inspection for the project. 111
Quality Management Responsibility Allocation: A summary of design and construction QM roles is shown in table 4-8. Table 4-8 â Summary of design and construction QM roles Responsibility allocation for design management tasks Agency personnel Consultant design staff Constructorâs preconstruction staff Agency-hired QA/oversight consultant Technical review of design deliverables â â â Checking of design calculations â Checking of quantities â Acceptance of design deliverables â Review of specifications â â â Approval of final construction plans & other design documents â Approval of progress payments for design progress â Approval of post-award design QM/QA/QC plans â Responsibility allocation for construction management tasks Agency personnel Consultant design staff Constructorâs construction staff Agency-hired QA/oversight consultant Technical review of construction shop drawings â Technical review of construction material submittals â Checking of pay quantities â Routine construction inspection â Quality control testing â Verification testing â Acceptance testing â Approval of progress payments for construction progress â Approval of construction post-award QM/QA/QC plans â Report of nonconforming work or punchlist. â Effective QM Practices: The following procurement and project n practices helped the project achieve enhanced quality: ï§ One-on-One Meetings - The Agency conducted one-on-one meetings with each Proposer to discuss issues and clarifications regarding the RFP and Proposerâs ATCs. ï§ Alternative Technical Concept (ATCs) Process - A process for pre-Proposal review of ATCs that conflict with the requirements for design and construction of the Project, or otherwise require a modification of the technical requirements of the Project. ï§ Competitive Range - The term âCompetitive Rangeâ means a list of the most highly rated Proposals, based on initial Technical Proposal ratings and evaluations of Price Proposals, which were judged by the Agency to have a reasonable chance of being selected for award. 112
ï§ Summary of Innovation and Enhanced Quality - The Proposers were to prepare a summary of no more than three pages that outlined the specific areas in which the Proposer had introduced innovation and provided enhanced quality in long-term performance, durability, or maintainability. ï§ Document Control - The QMP had to specify procedures for meeting documentation requirements, for document control and for the specific responsibilities of personnel to satisfy these requirements. ï§ Over-the-Shoulder Design Reviews - The DQM was to conduct design reviews. ï§ Milestone (30% and 60%) Reviews - The DQM was to conduct formal milestone reviews. ï§ Incentive/Disincentive Program 4.5.8 Hastings Bridge Project, Minnesota Project Name: TH61 Hastings Bridge Design-Build Project Name of Agency: Minnesota Department of Transportation (MnDOT) Location: T.H. 61 over the Mississippi River along the border of Washington and Dakota County, Minnesota within and near the City of Hastings. Project Delivery Method/Procurement/Contract Type: Design-Build/Best-Value/Lump Sum Project Description: The Project scope is to design and construct a new four-lane bridge over the Mississippi River, remove the existing 2-lane bridge, and construct the approaches on the north and south sides of the bridge. Project Quality Profile: The overall quality approach required the Contractor to develop, implement, and maintain a quality management system that encompassed the design and construction quality aspects, and documentation requirements for the Project. In addition, ATCs were used to permit the design-builder to literally negotiate the design quality criteria and the process for submitting and evaluating them was set forth in the Instructions to Proposers (ITP). 113
QAO: Figure 4-9 shows that the QAO for this project was Oversight. Project Acceptance Construction Quality Assurance Design Quality Assurance Design Quality Control Construction Quality Control Design Released for Construction Construction Released for Final Payment Independent Assurance (if reqâd) - functional audit -physical audit Owner Verification (if reqâd) Quality Assurance Independent Assurance (if reqâd) - functional audit -physical audit Design- Builderâs Responsibility Ownerâs Responsibility Figure 4-9 â Hastings Bridge QAO Model QA/QC Plans: The quality management process used on this project was a formal one that was project specific. The Contractorâs quality management system had to contain a Quality Manual (QM) that encompassed all Contract requirements with regard to design, construction, and documentation for all quality processes. The Quality Manual also included an Inspection and Testing Plan describing all of the proposed inspections and tests to be performed throughout the construction process. MnDOT had provided a Construction Quality Inspection and Testing Plan in the Quality Manual Template. The Contractor was to tailor the Inspection and Testing Plan to meet the Project requirements. 114
Quality Management Responsibility Allocation: A summary of design and construction QM roles is shown in table 4-9. Table 4-9 â Summary of design and construction QM roles Responsibility allocation for design management tasks Agency personnel Consultant design staff Constructorâs preconstruction staff Agency-hired QA/oversight consultant Technical review of design deliverables â â Checking of design calculations â Checking of quantities â Acceptance of design deliverables â Review of specifications â Approval of final construction plans & other design documents â Approval of progress payments for design progress â Approval of post-award design QM/QA/QC plans â Responsibility allocation for construction management tasks Agency personnel Consultant design staff Constructorâs construction staff Agency-hired QA/oversight consultant Technical review of construction shop drawings â â Technical review of construction material submittals â Checking of pay quantities Routine construction inspection â â Quality control testing â Verification testing â Acceptance testing â Approval of progress payments for construction progress â Approval of construction post-award QM/QA/QC plans â Report of nonconforming work or punchlist. â â Effective QM Practices: The following practices were implemented for the project and contributed to managing the quality of the project: ï§ ATC/PAE Process - Approved ATCs were known as Pre-Approved Elements (PAEs). MnDOT then conducted one-on-one meetings with proposers to discuss ATCs and the Proposers were able to incorporate one or more acceptable ATCs in to their proposal. ï§ Disciplinary Task Forces - Each task force will focus on a specific discipline of work. ï§ Over-the-shoulder design reviews - Informal examinations by MnDOT of design documents during the project design process. ï§ In-Progress Design Workshops - Throughout the design process, the Contractor or MnDOT could request in-progress design workshops to discuss and verify design progress and to assist the Contractor and/or its designer(s) in resolving design questions and issues. 115
ï§ Quality Oversight Visits - During the design process, MnDOT could make oversight visits to discuss and verify design progress and ascertain the overall progress of the Project with respect to the Contractorâs Quality Manual. ï§ Disincentive - Subject to MnDOTâs determination, MnDOT could assess the Contractor a $100-per-hour monetary deduction for failure to facilitate satisfactory progress or completion of the Work. 4.5.9 I-595 Express Corridor Improvements Project, Florida Project Name: I-595 Express Corridor Improvements Project Name of Agency: Florida Department of Transportation (FDOT) Location: Broward County, FL Project Delivery Method/Procurement/Contract Type: Public-Private-Partnership (P3), 2 step process for procurement, lump sum for design, construction, operate, and maintenance Project Description: The I-595 Express Corridor Improvements Project consists of the reconstruction of the I-595 mainline and all associated improvements to frontage roads and ramps from the I-75/Sawgrass Expressway interchange to the I-595/I-95 interchange, for a total length along I-595 of approximately 10.5 miles, and approximately 2.5 miles on Florida Turnpike from Peters Road to Griffin Road. The design and construction cost of the project is approximately $1.2 billion. Project Quality Profile: Because the project is PPP, and the concessionaire will be operating the project for 30 years, the concessionaire held the majority of the responsibility of the quality responsibilities, which equates to the acceptance quality assurance organizations, as shown in Figure 4-10. FDOT did hire several engineering consultants such as the design manager and the Oversight Construction Engineer Inspector (OCEI). Overall, the design managerâs responsibility was to make sure that the produced design met the requirements of the contract. FDOT and the design manager did have more involvement in the design when it came to elements of the project that were related to safety, such as bridges, and traffic control. The OCEI was responsible for conducting statistical sampling verification testing regarding the Concessionaireâs Construction Engineering Inspection. 116
QAO: Figure 4-10 shows that the QAO for this project was Acceptance. Project Acceptance Construction Quality Assurance Design Quality Assurance Design Quality Control Construction Quality Control Design Released for Construction Construction Released for Final Payment Independent Assurance (if reqâd) - functional audit -physical audit Owner Verification Testing Quality Assurance Independent Assurance (if reqâd) - functional audit -physical audit Ownerâs Responsibility Concessionairesâs Responsibility Independent Engineering Consultant Figure 4-10 â I-595 Express Corridor Improvements Project QAO QA/QC Plans: The concessionaire holds most of the risk associated with gaining a quality product, in that they are responsible for operation and maintenance of the corridor for 30 years after construction. To ensure that quality was a priority, part of the contract required submission and approval of a QA and QC plan for both design and construction before work began. The concessionaire created an overall QM plan, while the designer created the design QM, QA, and QC plans and the design builder created the construction QM, QA, and QC plans. 117
Quality Management Responsibility Allocation Summary For this case study independent questionnaires were received from the design builder (D), the concessionaire (C), the agency (A) and the engineer (E). Not all four responded the same way to the questionnaire, thus table 4-10 shows how each party responded. Table 4-10 â Summary of design and construction QM roles Responsible Party (select all that apply) Responsibility allocation for design management tasks Agency Design Staff Agency PM Staff Design Consultant Staff Constructorâs Pre-const. Staff Agency-hired QA/oversight Consultant Other, specify below Technical review of design deliverables 1 Checking of design calculations 2 Checking of quantities 2 Acceptance of design deliverables Review of specifications 2 Approval of final construction plans & other design documents Approval of progress payments for design progress 2 Approval of post-award design QM/QA/QC plans 2 Other: 1 â Is FDOT design construction; 2 â Is the Concessionaire Responsibility allocation for construction management tasks Agency Design Staff Agency PM Staff Design Consultant Staff Constructorâs Construction Staff Agency-hired QA/oversight Consultant Other, specify below Technical review of construction shop drawings Technical review of construction material submittals Checking of pay quantities Routine construction inspection Quality control testing Verification testing Acceptance testing Approval of progress payments for construction progress Approval of construction post- award QM/QA/QC plans Report of nonconforming work or punchlist. Other: Concessionaire and Concessionaire CEI D â Design Builder; A â Agency; C â Concessionaire; E â Engineer 118
Effective QM Practices: ï§ The dual Construction Engineer Inspection process where there is an oversight CEI (OCEI) hired by the agency and a CEI hired by the concessionaire (CCEI). The CCEI is responsible for the construction inspections on the project, while the oversight CEI audits the CCEI based on a statistical sampling process. This has been very successful, however because this was a new concept it took about a year to establish an understanding as to how the two CEIâs can best work together for the betterment of the project. ï§ During the construction phase unique electronic inspection and testing request were implemented as part quality management system for all subcontractors to follow. This process included converting emails to text messages to be received by people in the field without email. ï§ Two major procedures of the quality system, which affect all project work, are the witness and hold procedure and the testing and sampling (TSR) procedure, initiated by subcontractors, inspected by the design builder QC and verified by the CCEI. All work and materials used to advance the project are recorded and regulated by multiple parties (contractorâs QC staff, CCEI, OCEI). ï§ This project had many subcontractors that had never worked on a FDOT project, much less one that was a P3 project and had requirements for both FDOT and the concessionaire. Every subcontractor had to be trained on FDOT requirements and the Concessionaire team requirements, which included the submittal of quality management plans by the subs and material suppliers. The training also included concepts of different quality management processes/philosophies such as ISO 90001 etc. ISO was also included as reference materials to the training and development of the subs quality management plans. 4.5.10 SH 130 Turnpike Project, Texas Project Name: SH 130 Turnpike Project Exclusive Development Agreement Name of Agency: Texas Department of Transportation (TxDOT) â Texas Turnpike Authority Location: SH 130 through Travis and Williamson Counties, Texas Project Delivery Method/Procurement/Contract Type: PPP/Best-Value/Guaranteed Lump Sum (Exclusive Development Agreement). Project Description: State Highway (SH) 130 is an approximately 49-mile new toll-way extending from IH-35 near SH 195, north of Georgetown, Texas Southward to US Highway 183 southeast of Austin. SH 130 is a four-lane controlled-access toll-way with discontinuous frontage roads and directional interchanges where warranted. Work for this project included the design, right-of-way acquisition, utility adjustment, construction, and fifteen years of capital maintenance (if elected by TxDOT). Project Quality Profile: The SH 130 project QC/QA program consisted of four inter-dependent 119
components: the Quality Control (QC) Program, the Owner Oversight Program, the Independent Assurance (IA) Program, and the independent Construction Quality Assurance (CQA) Program. TxDOT developed a project-specific quality assurance program (QAP) for the SH130 project. In addition to safeguards in the QAP, the EDA had several measures to ensure the quality of workmanship and materials in the project. The measures were broken into three basic categories including quality control, acceptance testing and inspection, and owner verification. QAO: Figure 4-11 shows that the QAO for this project was Acceptance. Project Acceptance Construction Quality Assurance Design Quality Assurance Design Quality Control Construction Quality Control Design Released for Construction Construction Released for Final Payment Independent Assurance (if reqâd) - functional audit -physical audit Owner Verification Testing Quality Assurance Independent Assurance (if reqâd) - functional audit -physical audit Ownerâs Responsibility Concessionairesâs Responsibility Independent Engineering Consultant Figure 4-11 â SH 130 Turnpike QAO QA/QC Plans: The SH 130 was the first design-build highway infrastructure project in Texas where contractor QC testing was used in the acceptance decision for all project-produced materials. An enhancement to the previous owner verification process was the new three-tiered approach. In this approach Level 1 is applied to the tests which are strong indicators of performance and provides the highest level of confidence in the contractorâs QC testing. Level 2 is applied to tests that are secondary indicators of performance. Level 3 is applied to tests with extremely low test frequencies. 120
Quality Management Responsibility Allocation: A summary of design and construction QM roles is shown in table 4-11. Table 4-11 â Summary of design and construction QM roles Responsibility allocation for design management tasks Agency personnel Consultant design staff Constructorâs preconstruction staff Agency-hired QA/oversight consultant Technical review of design deliverables â â Checking of design calculations â â Checking of quantities â â Acceptance of design deliverables â â Review of specifications â Approval of final construction plans & other design documents â â Approval of progress payments for design progress â Approval of post-award design QM/QA/QC plans â Responsibility allocation for construction management tasks Agency personnel Consultant design staff Constructorâs construction staff Agency-hired QA/oversight consultant Technical review of construction shop drawings â Technical review of construction material submittals â Checking of pay quantities â Routine construction inspection â â Quality control testing â Verification testing â â Acceptance testing â Approval of progress payments for construction progress â Approval of construction post-award QM/QA/QC plans â â Report of nonconforming work or punchlist. â Effective QM Practices: Effective QM Practices that contributed to the success of the SH 130 Project are described below: ï§ Co-location: Due to the magnitude of the project, it was critical for all parties to be co- located on the project. ï§ Escalation Matrix: An escalation matrix was developed to provide a clear chain of command for escalating issues that could not be agreed upon, while promoting the resolution of issues at the lowest possible levels. ï§ Clarification Requests and Reports: Field clarification requests were used to clarify plans that had disconnects or discrepancies. Construction Deficiency Reports and Non- Conformance Reports were used to track non-conforming materials and workmanship. ï§ The Web-Based EDMS: The Electronic Laboratory Verification Information System (ELVIS) is a set of web-based data management and engineering analysis tools originally 121
developed to process material testing data and to transmit them electronically to TxDOT for statistical validation. To meet the project needs, ELVIS was further expanded to support CQAF construction inspection reporting and manage pavement surface ride quality. ï§ Industry Review Process: The industry review process included the development of a risk allocation table as a trade-off with the proposers and includes a reiterative cycle of subtasks. 4.6 Case Study Synthesis This section includes a series of tables summarizing the key details of all the case studies. The purpose of these tables is to provide a visual manner in which to compare the various case studies and recognize key trends. While these tables certainly do not tell the full story of any of the case studies and cannot capture all of the unique features of and methods used on each project, they are nonetheless useful for distilling each project into its key quality constituents. 4.6.1 Relationship between Delivery Method and QAO Table 4-12 lists the case studies along with their delivery, procurement, and payment methods and their identified QAO type as well. While it is theoretically possible to use a number of different QAO models for a given project delivery method, the case studies analyzed suggest that certain QAOs may be well suited for particular delivery methods. For example, while a project using the PPP delivery method could theoretically structure its QAO to include the owner in design or construction quality management roles, such a system was not found in the case studies. Instead, of the two PPP projects studied, both utilized the Acceptance QAO in which the owner only performs project acceptance and delegates the remaining QM roles and responsibilities. Table 4-12 â Delivery, Procurement, and Payment Methods and QAO # Agency Name QAO Delivery Method Procurement Method Payment Provisions 1 WSDOT George Sellar Bridge Deterministic DBB w/eci Best value Lump sum 2 ODOT Willamette River Bridge Deterministic CMGC Best value GMP 3 TriMet Portland Transit Mall Deterministic CMGC Best value GMP 4 USACE Tuttle Creek Dam Deterministic CMGC QBS Prog. GMP 5 UDOT Mountain View Corridor Assurance CMGC Best value GMP 6 CDOT US 160 4th Lane Addition Oversight Mod. DB Low bid Lump sum 7 UDOT I-15 Widening-Beck Street Oversight DB Best value Lump sum 8 MnDOT Hastings River Bridge Oversight DB Best value Lump sum 9 FDOT I-595 Express Corridor Acceptance PPP Best value Lump sum 10 TxDOT SH130 Turnpike Extension Acceptance PPP Best value Lump sum GMP â Guaranteed Maximum Price; QBS â Quality Based Selection; Prog. GMP â Progressive GMP, multiple bid packages with separate GMPs for each package All three of the case studies using the DB delivery method used the Oversight QAO model. The Oversight QAO leaves all design and construction QA and QC functions in the hands of the designer, contractor, or design-builder. While an owner could retain a QA function if desired as 122
found in the Assurance QAO, this was not found in the case studies examined. Similarly, while a project using DBB delivery could potentially allow the contractor to assume a quality assurance role as found in an Assurance QAO, the baseline QAO and the one used on the WSDOT project studied was the Deterministic QAO. The Deterministic arrangement of quality roles accurately reflects the baseline QM system and it would be expected to be found on most DBB projects. In contrast, the case studies, which used the CMGC delivery method, showed slightly more variation in their QAOs. While three of the case studies utilized a Deterministic QAO, the fourth, Mountain View Corridor, made use of an Assurance QAO. The Assurance QAO allows the designer to perform its own design QC without interference from the owner and its use on the Mountain View Corridor project may reflect UDOTâs long period of experience and comfort with the CMGC delivery method. Table 4-13 provides a succinct summary of the QM roles and responsibilities, which must be assigned under each QAO model. Only four of the five QAO models were found in the case studies as none of them made use of the Variable QAO. The QAOs show very little variation for the most part. However, case studies 2 and 3, which both used the CMGC delivery method, as shown in table 4-13 show some deviation from the other case studies using Deterministic QAOs. The primary difference is the sharing of the design QC function between the owner, designer, and builder. In fact, were it not for the sharing of this role, these case studies would have been listed as using an Assurance QAO. On each of these projects however, the owner wanted to maintain an active role in design QC despite outsourcing most of the projectsâ design. 123
Table 4-13 â Summary of Varying Quality Roles Quality Management Roles and Responsibilities # QAO Project Acceptance Design QC Design QA Const. QC Const. QA Indep. Assurance OVT O D B O D B O D B O D B O D B O D B D B B 1 Deterministic â â â â â â 2 Deterministic â â â â â â â â â 3 Deterministic â â â â â â â â â 4 Deterministic â â â â â â 5 Assurance â â â â â â â 6 Oversight â â â â â â 7 Oversight â â â â â â â 8 Oversight â â â â â â â 9 Acceptance â Conc Conc Conc Conc Conc â 10 Acceptance â Conc Conc Conc Conc Conc â O â Owner; D â Designer; B â Builder; Conc â Concessionaire 4.6.2 Documents Required Before Contract Award Quality management is not a static process but rather is affected by decisions made at all points along a projectâs timeline from conception to ribbon cutting. One milestone where decisions must be made that will affect the overall quality of the project is just before the release of procurement documents like RFQs and RFPs. Table 4-14 lists the documents that were required to be submitted by interested designers, builders, or design-builders before the award of any contracts for design or construction. Those documents marked with a plus sign were specifically listed as being evaluated as part of the award decision. 124
Table 4-14 â Summary of Required pre-Award Submittals Required Proposal/Bid Package Submittals Case Study Number 1 2 3 4 5 6 7 8 9 10 Qualifications of Design Quality Manager â+ â+ â+ â+ â+ â+ Qualifications of Construction Quality Manager â â+ â+ â+ â+ Qualifications of other QM personnel â+ â+ â+ â+ â+ â+ Design quality management plan â+ â+ â+ â+ â+ Design criteria checklists â+ â+ â+ â+ Construction quality management/control plan â+ â+ â+ Construction testing matrix â+ â Quality-based incentive/disincentive features â+ â Warranties â â â+ +: Evaluated to make award decision(s) Four case studies required submission of one of these documents or less before making award decisions. Of these four, three, with the exception of the sole DBB project, required several of these documents were after the award. For the remaining six case studies, the most common documents required were the qualifications of design quality managers (6 case studies), of other QM personnel (6), of the construction quality manager (5), and the design QMP (5). From this information, the owners of these six projects valued incorporating quality into their projects from the start. 4.6.3 Inventory of Emerging Tools Each of the case studies furnished a number of QM tools considered non-traditional that project participants indicated as beneficial to their project. Table 4-15 lists the primary tools identified and divides them into two groups: those used before the award of design or construction contracts and those used after. Use of the pre-award tools can help to ensure clarity in the procurement process, to modify project requirements, and to adjust quality requirements when it is prudent to do so. Owner, design-builders and concessionaires can use the post-award tools to improve aspects of QM along all the phases of a project after selecting a designer and contractor. One of the reasons for dividing the tools in this manner was to draw attention to the importance of when to incorporate quality in to a project. Traditional QM methods are reactive and emphasize QC testing to evaluate quality after completion of portions of a project. Most of the emerging tools discovered in the case studies are used not to measure if quality standards were met, as in QC testing, but rather to plan for and build quality into the project long before any designs are complete or any construction is started. Later research efforts will explore under what circumstances these tools might be used and with which QAOs they are compatible. 125
Table 4-15 â List of Emerging Alternative QM Tools Pre-award Tools Post-award Tools ï§ Owner led o Pre-bid meeting with focus on quality o Industry review of draft RFP with focus on quality o ISO 9000 certification for organization, project, or team member o Alternative QM approaches in procurement o Quality based selection of contractors/subcontractors (project- specific prequalification) o Use of warranties (performance or materials) ï§ Contractor led o One-on-one meetings during procurement with a focus on alternative quality o Contractor proposed alt. quality standards/specification deviations o âRed Flagâ review of standard specs o Alternative Technical Concepts (ATCs) Design process ï§ Design review: o External contractor panel input o Independent party review (agency, staff extension) o Over-the-shoulder agency reviews o In-progress design workshops o Discipline task force (parallel entire project) Construction process ï§ Teaming: o Formal partnering with regulatory agencies o Formal team partnering/goal-setting process o Co-location of QM personnel o Discipline task force (parallel entire project) o No low bid requirement for subcontractors o Use of dual CEI/OCEI roles ï§ Process control: o Innovation in witness and hold points o Continuous internal process audit o Real time electronic QM information management o Financial incentive/disincentives for quality o Contractor âcontrolledâ QC testing o Innovation in clarification reports ï§ Training: o ISO 9000 training of sub-contractors o Project-specific QM team training OCEI â Oversight CEI 4.7 Summary As seen in this chapter, great time and consideration was given to the identification and selection of the case studies used for this report and to ensuring that they were conducted using a rigorous and thorough methodology. After conducting the case studies, the information gathered was distilled into the full case studies found in the appendices and synthesized in the tables at the end of this chapter. Case studies were examined for their successes related to alternative QM as well as a breakdown of the primary design and construction QM roles and responsibilities. This information was then used to craft a QAO diagram for each case study which was then matched to one of the five primary QAOs identified in Chapter 3. Each of the ten case studies conducted for this project provided a wealth of information regarding the implementation of alternative QMSs and a number of innovative alternative QM tools. 126
TRB’s National Cooperative Highway Research Program (NCHRP) Web-Only Document 212: Alternative Quality Management Systems for Highway Construction documents the research process, data collection and analysis used to develop NCHRP Report 808: Guidebook on Alternative Quality Management Systems for Highway Construction .
READ FREE ONLINE
Welcome to OpenBook!
You're looking at OpenBook, NAP.edu's online reading room since 1999. Based on feedback from you, our users, we've made some improvements that make it easier than ever to read thousands of publications on our website.
Do you want to take a quick tour of the OpenBook's features?
Show this book's table of contents , where you can jump to any chapter by name.
...or use these buttons to go back to the previous chapter or skip to the next one.
Jump up to the previous page or down to the next one. Also, you can type in a page number and press Enter to go directly to that page in the book.
To search the entire text of this book, type in your search term here and press Enter .
Share a link to this book page on your preferred social network or via email.
View our suggested citation for this chapter.
Ready to take your reading offline? Click here to buy this book in print or download it as a free PDF, if available.
Get Email Updates
Do you enjoy reading reports from the Academies online for free ? Sign up for email notifications and we'll let you know about new publications in your areas of interest when they're released.
Academia.edu no longer supports Internet Explorer.
To browse Academia.edu and the wider internet faster and more securely, please take a few seconds to upgrade your browser .
Enter the email address you signed up with and we'll email you a reset link.
- We're Hiring!
- Help Center
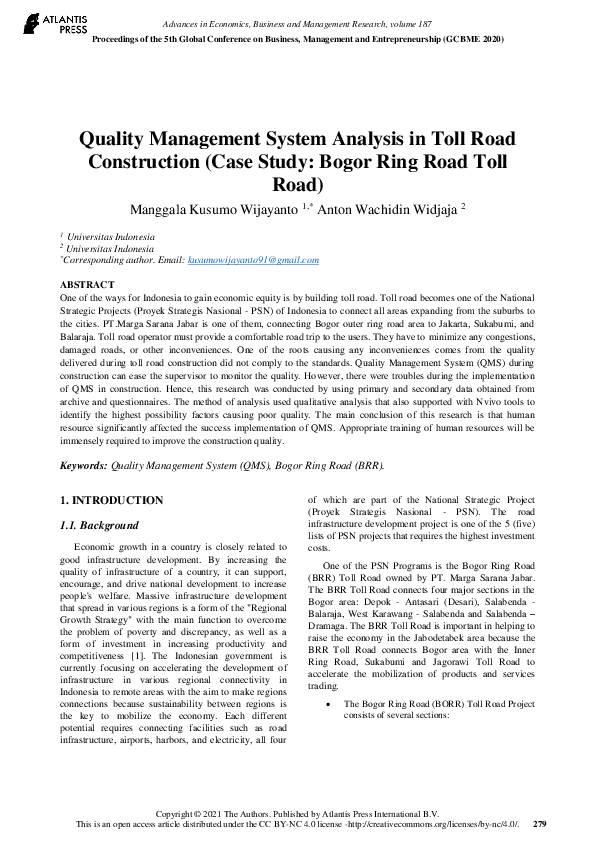
Quality Management System Analysis in Toll Road Construction (Case Study: Bogor Ring Road Toll Road)
Proceedings of the 5th Global Conference on Business, Management and Entrepreneurship (GCBME 2020)
Related Papers
Abbas Afshar
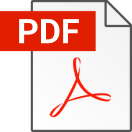
International Journal of Engineering Sciences and Research Technology
Abhaysinha Shelake
Viviana Lopez Torres Gordillo
shayne cabrera
Wan Yusoff Wan Mahmood
This chapter highlighted the results on the evaluation of the QMS implementation in the case project, Kuala Lumpur International Airport (KLIA). It first discussed the opinion of the experts gathered through a questionnaire regarding the propositions derived from the literature ...
Procedia - Social and Behavioral Sciences
Costache Rusu
International Journal of Productivity and Performance Management
Sanaul Chowdhury
Automation in Construction
Irtishad Ahmad
IJESRT Journal
Quality control in construction is a vital element that should be given importance and in-depth assessment. This study looked into the quality control management of the road infrastructure projects of the Department of Public Works and Highways (DPWH) – Leyte Second District Engineering (2 nd LED) Office for Calendar Years 2011- 2015. Utilizing qualitative-descriptive research design, the study involved 30 Implementers, 30 Contractors, and 50 Beneficiaries of the road projects. Results of the study show that all road infrastructure projects were properly implemented, the quality control management were effective, material requirements were well complied, testing requirements were impressively complied, and the construction requirements had been strictly followed and remarkably complied. On project management, the primary problems or issues met by Project Implementers were on the need of the Resident Engineer to be present "at all times", Contractors being required to hire Materials Engineers "on site", and the Contractors being responsible for the quality control of all materials.Proper supervision, standard materials, experienced workmen, and proper coordination between technical men, among others, were the primary problems during project implementation.The primary problem on project evaluation fell on strictly administering quality management, keeping materials quality control documents, and work progress/accomplishments.Project Implementers must successfully manage and control the work to the highest level by identifying, tracking, managing, and resolving project issues; and they need to adhere to an open communication policy. Stakeholders need to be involved in the identification, implementation and evaluation of projects.DPWH-2 nd LED Office needs to require technical and non-technical personnel to adopt “quality circles” where they will meet regularly to make suggestions for continuous quality control improvement; and hire additional technical personnel, rotate project assignments of the technical personnel, and minimize or remove subcontractors with minor contracts who cannot come up with quality infrastructure road projects.
Journal of Management in Engineering
Mark Federle , Charles Jahren
RELATED PAPERS
Ecotoxicology (Springer)
Dr. Laxmi K A N T Bhardwaj
International Journal of Hygiene and Environmental Health
Anna Mölter
TAPROBANICA: The Journal of Asian Biodiversity
Senarathge Weerawardhena
Mediterranean Journal of Chemistry
Maria R Hepel
Chasqui. Revista Latinoamericana de Comunicación
Diana Sofía Santos
The Urban Book Series
Annals of Botany
Akihiro Sumida
Birgitta Söder
Muhammad Shahidul Haque
Gabriel Cirino Gerena
Significação: Revista de Cultura Audiovisual
Anales de Antropología
Linda Rosa Manzanilla Naim
International Journal of Analytical, Experimental and Finite Element Analysis (IJAEFEA)
Yash Tiwari
Enciclopédia Biosfera
Yasmim Santos
Jurnal Pendidikan Matematika Undiksha
Zaid Zainal
V Jornadas de Enseñanza e Investigación Educativa en el campo de las Ciencias Exactas y Naturales (Ensenada, 8 al 10 de mayo de 2019)
Mariela Paula Bayardo
Management Science Research Journal
Nani Suhartini
Juan Yovani Telumbre-Terrero
International Journal of Agronomy
justin Chipomho
Journal of dairy science
American Journal of Mechanics and Applications
Hasan OUAKHIR
Ruchini Jayasinghe
Jurnal Disrupsi Bisnis
NURMIN ARIANTO
Journal of Agricultural and Food Chemistry
Fatima Jibril
- We're Hiring!
- Help Center
- Find new research papers in:
- Health Sciences
- Earth Sciences
- Cognitive Science
- Mathematics
- Computer Science
- Academia ©2024
- Help & FAQ
Quality management case studies in the UK construction industry
- Mechanical Engineering
Research output : Contribution to journal › Article
- construction industry
Access to Document
- 10.1080/14783360802224545
Fingerprint
- Quality Management Business & Economics 100%
- Construction Industry Business & Economics 87%
- Internal Communication Business & Economics 36%
- Construction Sector Business & Economics 33%
- Construction Companies Business & Economics 33%
- Customer Needs Business & Economics 28%
- Manufacturing Business & Economics 28%
- Total Quality Management (TQM) Business & Economics 27%
T1 - Quality management case studies in the UK construction industry
AU - Delgado-Hernandez, DJ
AU - Aspinwall, Elaine
PY - 2008/1/1
Y1 - 2008/1/1
N2 - The UK construction sector has been challenged to adopt manufacturing concepts to improve its performance. Total Quality Management (TQM) has been suggested as one approach that could bring about benefits to the industry. However, to date, the associated literature offers little specific information relating to current practices in the UK. To determine how construction companies deal with quality issues within their processes, seven case studies were performed. The information collected shows that the industry has begun to take up the challenge and, as a result, companies have won repeat business, increased their market shares and improved their customer satisfaction levels. Nevertheless, participant companies also recognised that there are still shortcomings in their practices such as lack of internal communication, ineffective decision-making processes and poor identification of customer needs.
AB - The UK construction sector has been challenged to adopt manufacturing concepts to improve its performance. Total Quality Management (TQM) has been suggested as one approach that could bring about benefits to the industry. However, to date, the associated literature offers little specific information relating to current practices in the UK. To determine how construction companies deal with quality issues within their processes, seven case studies were performed. The information collected shows that the industry has begun to take up the challenge and, as a result, companies have won repeat business, increased their market shares and improved their customer satisfaction levels. Nevertheless, participant companies also recognised that there are still shortcomings in their practices such as lack of internal communication, ineffective decision-making processes and poor identification of customer needs.
KW - construction industry
U2 - 10.1080/14783360802224545
DO - 10.1080/14783360802224545
M3 - Article
SN - 1478-3371
JO - Total Quality Management and Business Excellence
JF - Total Quality Management and Business Excellence

IMAGES
VIDEO
COMMENTS
A study of the literature and of surveys conducted in the USA indicated that management commitment to quality and to continuous quality improvement is very important; construction industry ...
The ISO 9001 Quality Management System was introduced in 1987 and is now one of the most widely adopted ... the extent of regulatory decoupling and its impact on the effectiveness of implementation of the ISO 9001 QMS in 3 case study construction companies. This paper proceeds as follows: in the next section we review the literature on Quality ...
In the light of Quality Management System (QMS), a case study was conducted in Engineers India Ltd. (EIL), who are one of the renowned project management consultants in the country, to find out how EIL takes care of the above-mentioned factors, along with others, to support their QMS in construction project management.
The following are the previous research review based on quality management system in construction industry. Abdul Hakim Muhammad et al. (2006) ... and a case study is performed using content review tool to validate the questionnaire. They concluded by interviewing . Chirag Patel QUALITY MANAGEMENT SYSTEM RT&A, Special Issue № 1 (60)
This study wa s carried out in order to e valuate the impact of quality. management system installation on the main f actors of a construction project (cost, time, quality/scope) in a sample of ...
Total quality management (TQM) has been recognized as a successful management philosophy in the manufacturing and service industries. TQM can likewise be embraced in the construction industry to help raise quality and productivity. Two case studies of construction companies showed how TQM can be successfully implemented in the construction ...
A quality system should be implemented in every aspect of a project, such as the project document, materials, testing, construction process, etc. Involving a case study in this paper will assist ...
The approval is by the Consultant as he is the designer of the project. A Case Study on Quality Management System in Construction Project 51 PROCESS CONTROL All parties indicate that the output of the elements of quality planning and resources management are the input for the process control such as work programme, cost programme etc.
This paper explores the role of quality management system (QMS), such as ISO 9000, and total quality management, and their approaches in construction industry. The aim is to determine if these systems have the potential to generate new knowledge for improving quality management practices and outcomes in construction projects. This paper reviews all the prior literatures relevant to QMS in ...
These translate into higher buildability, efficiency and cost-effectiveness for the condominium project. The case study therefore concludes that the ISO 9000 quality management system can function as an effective and appropriate working platform for operationalising buildability principles at both the design and construction stage of a project.
This chapter highlighted the results on the evaluation of the QMS implementation in the case project, Kuala Lumpur International Airport (KLIA). It first discussed the opinion of the experts gathered through a questionnaire regarding the propositions derived from the literature review. Then it followed with the discussion on the data collected from the PQP of the construction team and the ...
Quality management is a key pillar of overall construction project management, and is often the difference between company's success and failure. Quality management in construction is the policies, processes and procedures put in place (typically by management) to improve an organisation's ability to deliver quality to its customers - whether ...
The UK construction sector has been challenged to adopt manufacturing concepts to improve its performance. Total Quality Management (TQM) has been suggested as one approach that could bring about benefits to the industry. However, to date, the associated literature offers little specific information relating to current practices in the UK.
A quality management system must be maintained, evaluated, monitored and enhanced regularly. ... (2009), " Cost of quality in Dubai: an analytical case study of residential construction projects ", International Journal of Project Management, Vol. 27 No. 5, pp. 501-511, doi: 10.1016/j.ijproman.2008.07.006.
CDOT performed testing on all materials; it appears that quality management system for the construction was heavily directed by the agency. The lack of a design builder created construction QC plan is further evidence that the construction quality management was directed by CDOT. 107
The Principles of Quality Management System Quality Management System (QMS) is the interaction of people, processes and documentation to meet both customers‟ stated and implied needs (Mohammed, A. H. 2006 and Abdullah, M. N. 2006). Figure 1.0: Approaches to conformance in Quality Management
Construction Phase. ♦ Majority of the contractors is of the opinion that. management of quality is very important at the. execution stage of project. This leads to the fact. that no matter how ...
case study on quality management sysem (quality assurance and quality control) in construction projects by budiman amat @inproceedings{Amat2014CASESO, title={CASE STUDY ON QUALITY MANAGEMENT SYSEM (QUALITY ASSURANCE AND QUALITY CONTROL) IN CONSTRUCTION PROJECTS by BUDIMAN AMAT}, author={Budiman Amat and Idris Othman}, year={2014}, url={https ...
Quality control in construction is a vital element that should be given importance and in-depth assessment. This study looked into the quality control management of the road infrastructure projects of the Department of Public Works and Highways (DPWH) - Leyte Second District Engineering (2 nd LED) Office for Calendar Years 2011- 2015.
The study aims to carry out an exploratory study of the application of Construction 4.0 and Industrial 4.0 in quality management of building works and the development of Lean-based quality ...
Evaluation of Quality during Construction Projects: A Case Study of Pakistan quality can be controlled from him [27]. The momentum of whole management system depends on the combined effort or team work. The failure or success of any organization depends on caliber of leadership [28]. 2.2 Quality Control Standards
The parameters included in the developed automated QC system have been selected according to the customized QC checklist of the case study project. The developed system is adaptable, allowing for the inclusion of additional parameters and points if needed. Figure 6 shows an image of the case study BIM models utilized in this study. As ...
The UK construction sector has been challenged to adopt manufacturing concepts to improve its performance. Total Quality Management (TQM) has been suggested as one approach that could bring about benefits to the industry. However, to date, the associated literature offers little specific information relating to current practices in the UK.
During its 12 years of life, the company has implemented various quality initiatives including: a. certified to ISO 9001: 2000, OHSAS 18001 and ISO 14001 in order to control its processes in all ...